Highly efficient ore dressing system of medium-low class aluminium ore
A technology of low-grade bauxite and mineral processing methods, applied in chemical instruments and methods, flotation, wet separation, etc., can solve the problems of large consumption of chemicals and achieve low production costs, stable operation, and stable indicators
- Summary
- Abstract
- Description
- Claims
- Application Information
AI Technical Summary
Problems solved by technology
Method used
Image
Examples
example 1
[0047] Example 1: Grinding the pulverized raw materials with a ball mill. The working conditions of the ball mill are as follows: ball mill specification Φ305×305mm, wet ball mill grinding, spherical medium diameter and ratio are Φ30mm: Φ20mm: Φ15mm = 30%: 50%: 20%, medium filling rate is 40%, material-ball ratio is 1.2, the speed rate is 91%, the grinding weight concentration is 70%, the grinding time is 8 minutes, and the grinding fineness reaches -200 mesh, accounting for 48.22%. The resulting product is made into a slurry with a weight concentration of 30%, and is classified by a hydrocyclone to control d 50 The structural parameters and operating parameters of the hydrocyclone are as follows: diameter 50mm, ore feeding port diameter 10mm, overflow pipe diameter 13mm, sand outlet diameter 6mm, cone angle 20°, ore feeding pressure 0.06MPa, here Under the conditions, the ratio of aluminum to silicon is 9.18, the yield is 43.34%, and the Al 2 o 3 The recovery rate is 47.05...
example 2
[0048] Example 2: Grinding fineness -200 mesh accounts for 52.55%, and the grinding product is made into pulp with a weight concentration of 40%. The feeding pressure of the hydrocyclone in the classification operation is 0.09MPa, and the feeding weight concentration is 40%; desliming, The ore feeding pressure of the hydrocyclone in the concentration operation is 0.12MPa, the ore weight concentration is 30%; the weight concentration of the flotation pulp is 35%, and the flotation time is 8 minutes. The collector uses sodium oleate, and the dosage is 825g / t raw ore; the dispersant Sodium carbonate is used in an amount of 1.8kg / t raw ore to obtain flotation concentrate. Other conditions are the same as Example 1, and the available aluminum-silicon ratio is 9.47, yield 43.23%, Al 2 o 3 Coarse grade concentrate with a recovery rate of 47.89%, the aluminum-silicon ratio of the mixed concentrate is 9.38, Al 2 o 3 The recovery rate was 88.56%.
example 3
[0049] Example 3: Grinding fineness -200 mesh accounts for 54.96%, and the grinding product is made into slurry with a weight concentration of 50%, for classification operations, the feeding pressure of the hydrocyclone is 0.12MPa, and the feeding weight concentration is 50%; desliming , Concentration operation hydrocyclone feed pressure 0.16MPa, feed ore weight concentration 20%; flotation pulp weight concentration 40%, flotation time 10min, the collector uses a mixture of oxidized paraffin soap and sodium oleate (oxidized paraffin Soap:sodium oleate=1:1, weight ratio), the dosage is 1000g / t raw ore; the dispersant uses sodium carbonate, the dosage is 2.0kg / t, to obtain the flotation concentrate. Other conditions are the same as Example 1, and the available aluminum-silicon ratio is 9.28, productive rate 43.52%, Al 2 o 3 Coarse grade concentrate with a recovery rate of 47.16%, the aluminum-silicon ratio of the mixed concentrate is 9.57, Al 2 o 3 The recovery rate was 88.11...
PUM
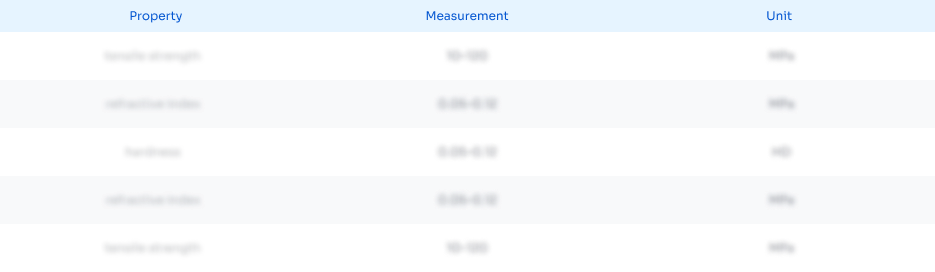
Abstract
Description
Claims
Application Information

- R&D
- Intellectual Property
- Life Sciences
- Materials
- Tech Scout
- Unparalleled Data Quality
- Higher Quality Content
- 60% Fewer Hallucinations
Browse by: Latest US Patents, China's latest patents, Technical Efficacy Thesaurus, Application Domain, Technology Topic, Popular Technical Reports.
© 2025 PatSnap. All rights reserved.Legal|Privacy policy|Modern Slavery Act Transparency Statement|Sitemap|About US| Contact US: help@patsnap.com