Preprocessing technology for processing integral key shaft
A spline shaft and pretreatment technology, which is applied in the field of spline shaft processing and pretreatment, can solve the problems of uneven hardness, increased frequency of scrapped tools, and wear of rolling tools, so as to improve production efficiency and economic benefits, and speed up product flow. time, the effect of improving hardness uniformity
- Summary
- Abstract
- Description
- Claims
- Application Information
AI Technical Summary
Problems solved by technology
Method used
Image
Examples
Embodiment 1
[0009] Embodiment 1: The pretreatment process of the spline shaft of the present invention adopts the surface induction annealing process, the blank of the spline shaft 1 adopts the American standard SAE1045 steel, and the equipment adopts the intermediate frequency quenching machine GK1080A, and the specific process is: the intermediate frequency quenching machine is set The fixed power is 80-90 kilowatts, set 10-15 Hz on the inverter, and set the moving distance of the blank. During induction annealing, the induction annealing area 1-1 of the general spline shaft (that is, the spline processing part) is as follows: figure 1 shown. The surface part of the blank to be splined is heated by induction above A C3 (Generally between 700-720°C) above 60°C. At this time, the transformation ratio is 12:1, the operating power of the equipment is 80-90KW, the induction coil moves from top to bottom in the front section of induction annealing area 1-1, and the moving speed is 5HZ, and t...
Embodiment 2
[0011] Embodiment 2: The spline shaft processing pretreatment process of the present invention adopts the surface induction annealing process, and the blank of the spline shaft adopts No. 45 steel of the national standard. higher than A C3 Above 50°C temperature, the power of the equipment is 80-90KW. In the front section of the induction annealing area 1-1, the induction coil moves from top to bottom with a moving speed of 5HZ and a moving speed of 4.5HZ in the last 15mm. Keep warm for 1 hour; that is, slowly cool in the asbestos cylinder to about 300°C, and then air cool to normal temperature.
Embodiment 3
[0012] Embodiment 3: The spline shaft processing pretreatment process of the present invention adopts the surface induction annealing process, and the blank of the spline shaft adopts No. 45 steel of the national standard. higher than A C3 The temperature above 80°C, the operating power of the equipment is 80-90KW, the front section of the induction annealing area 1-1, the induction coil moves from top to bottom, the moving speed is 5HZ, and the moving speed is 4.5HZ in the last 20mm; heat preservation for 2 hours, That is, it is slowly cooled to about 300°C in the asbestos cylinder, and then air-cooled to normal temperature.
PUM
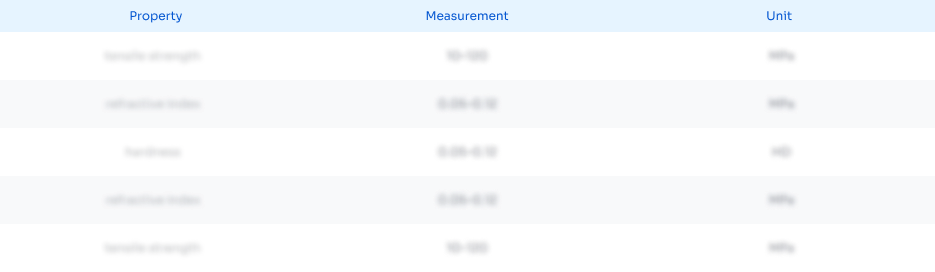
Abstract
Description
Claims
Application Information

- R&D
- Intellectual Property
- Life Sciences
- Materials
- Tech Scout
- Unparalleled Data Quality
- Higher Quality Content
- 60% Fewer Hallucinations
Browse by: Latest US Patents, China's latest patents, Technical Efficacy Thesaurus, Application Domain, Technology Topic, Popular Technical Reports.
© 2025 PatSnap. All rights reserved.Legal|Privacy policy|Modern Slavery Act Transparency Statement|Sitemap|About US| Contact US: help@patsnap.com