Kinematics control method for complex-curved-surface five-axis numerical control machining cutter vectors
A technology of complex curved surface and control method, which is applied in the field of precise and efficient machining of complex curved surface five-axis CNC machine tools
- Summary
- Abstract
- Description
- Claims
- Application Information
AI Technical Summary
Problems solved by technology
Method used
Image
Examples
Embodiment Construction
[0064] The specific implementation manner of the present invention will be described in detail in conjunction with the accompanying drawings and technical solutions.
[0065] As the surface shape becomes more and more complex, in the five-axis CNC machining of complex surfaces, the drastic change of the tool axis vector causes the vibration of the machine tool, and even exceeds the movement limit of the machine tool's rotary feed axis, which affects the quality of surface processing and limits the performance of the machine tool. The present invention utilizes the surface / curve modeling method and its parameter calculation method in differential geometry, the coordinate system transmission mode and coordinate conversion calculation method in machine tool kinematics, and establishes the motion of the rotary feed axis of a five-axis CNC machine tool according to the geometric characteristics of complex surfaces Parameter calculation method, to determine the relationship between t...
PUM
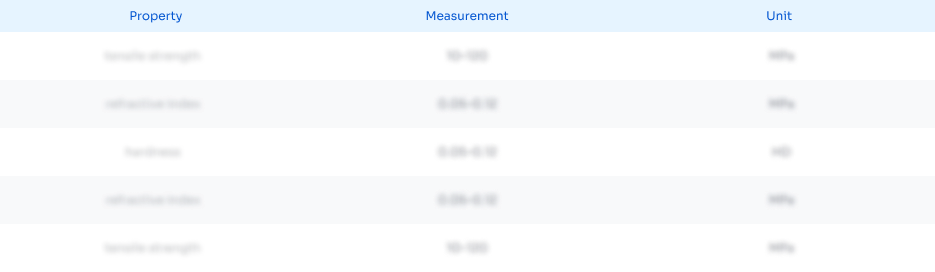
Abstract
Description
Claims
Application Information

- R&D
- Intellectual Property
- Life Sciences
- Materials
- Tech Scout
- Unparalleled Data Quality
- Higher Quality Content
- 60% Fewer Hallucinations
Browse by: Latest US Patents, China's latest patents, Technical Efficacy Thesaurus, Application Domain, Technology Topic, Popular Technical Reports.
© 2025 PatSnap. All rights reserved.Legal|Privacy policy|Modern Slavery Act Transparency Statement|Sitemap|About US| Contact US: help@patsnap.com