Method for preparing m-phthaloyl chloride in high purity
A high-purity isophthaloyl chloride technology, which is applied in the field of preparation of high-purity isophthaloyl chloride by chlorination, can solve the problems of high production cost, long production cycle, and complicated process of isophthaloyl chloride. To achieve the effect of highlighting substantive features, low production cost, and simple refining process
- Summary
- Abstract
- Description
- Claims
- Application Information
AI Technical Summary
Problems solved by technology
Method used
Examples
Embodiment 1
[0014] Embodiment 1, first 480 kilograms of chlorobenzene, 100 kilograms of isophthalic acid and 10 kilograms of N, N-dimethylformamide are added in the batching tank, close chlorobenzene, isophthalic acid and N, N-dimethylformamide Base formamide feed valve, start stirring to mix the raw material liquid, use the slurry pump to transport the mixed slurry raw material into the reactor, close the slurry pump and feed valve; open the stirring device of the reactor, and feed the liquid Heat to 75°C, open the exhaust condenser cooled with chilled water on the upper part of the reactor, open the tail gas exhaust valve, and then open the chlorinating agent COCl 2 Feed valve to regulate gaseous COCl 2 The flow rate is 100L / h, the temperature of the feed liquid gradually rises to 85°C, and is maintained until the end of the reaction. During the reaction, the slurry in the reaction liquid becomes less and less, the color of the solution gradually turns yellow, and there is basically no ...
Embodiment 2
[0015] Embodiment 2, earlier 480 kilograms of isophthaloyl dichloride, 100 kilograms of isophthalic acid and 10 kilograms of N, N-diethylformamide join in the batching tank, close isophthaloyl dichloride, isophthalic acid and N, N-dimethylformamide feed valve, start stirring to mix the raw material liquid, use the slurry pump to transport the mixed slurry raw material into the reactor, close the slurry pump and the feed valve; open the reactor Stirring device, heat the feed liquid to 50°C, open the exhaust condenser cooled with chilled water on the upper part of the reactor, open the tail gas exhaust valve, and then open the SOCl 2 Feed valve, regulate SOCl 2 The flow rate is 100L / h, the temperature of the feed liquid rises gradually to 90°C, and remains until the end of the reaction. During the reaction, the slurry in the reaction liquid becomes less and less, the color of the solution gradually turns yellow, and there is basically no solid in the reaction liquid For particl...
Embodiment 3
[0016] Embodiment 3, first 240 kilograms of dichlorobenzene, 240 kilograms of xylene, 100 kilograms of isophthalic acid and 10 kilograms of N, N-diethylformamide are added in the batching tank, close the dichlorobenzene, xylene, m- Phthalic acid and N, N-dimethylformamide feed valves, start stirring to mix the raw material liquid, use the slurry pump to transport the mixed slurry raw materials into the reactor, and close the slurry pump and feed valve; Turn on the stirring device of the reactor, heat the feed liquid to 30°C, open the exhaust condenser cooled with chilled water on the upper part of the reactor, open the tail gas exhaust valve, and then open the POCl 3 Feed valve, regulating POCl 3 The flow rate is 100L / h, the temperature of the feed liquid is gradually raised to 50°C, and kept until the end of the reaction. During the reaction, the slurry in the reaction liquid becomes less and less, the color of the solution gradually turns yellow, and there is basically no so...
PUM
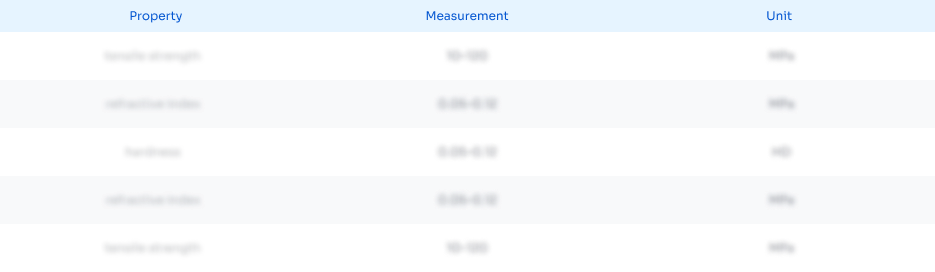
Abstract
Description
Claims
Application Information

- R&D
- Intellectual Property
- Life Sciences
- Materials
- Tech Scout
- Unparalleled Data Quality
- Higher Quality Content
- 60% Fewer Hallucinations
Browse by: Latest US Patents, China's latest patents, Technical Efficacy Thesaurus, Application Domain, Technology Topic, Popular Technical Reports.
© 2025 PatSnap. All rights reserved.Legal|Privacy policy|Modern Slavery Act Transparency Statement|Sitemap|About US| Contact US: help@patsnap.com