Method of mfg. semiconductor device for improving adhesion property of copper metalic butt barrier layer
A semiconductor and copper metal technology, applied in the field of manufacturing semiconductor devices with copper metal layers, can solve problems such as fracture, peeling, defective lines, etc., to prevent adhesion decline, prevent stress-induced voids, and prevent stress migration and electron migration decrease the effect of
- Summary
- Abstract
- Description
- Claims
- Application Information
AI Technical Summary
Problems solved by technology
Method used
Image
Examples
Embodiment Construction
[0016] in such as Figure 2A After forming an unillustrated semiconductor element on the shown semiconductor substrate 10, a 100-300 nm thick oxide film (SiO 2 film), as an interlayer insulating film. In SiO 2 A SiCN film 14 with a thickness of 10-150 nm is formed on the film 12 as an etching limiting film to improve the processability of the circuit. Further, on the SiCN film 14, SiO with a thickness of 100-1800 nm is formed. 2 The film 16, as an insulating film, is used to form wiring. Hereinafter, the SiCN film serving as an etching limiting film is referred to as a "limiting SiCN film". Also, in the process of forming semiconductor elements such as transistors, resistors, capacitors, etc., and wiring for connecting the semiconductor elements later on the semiconductor substrate, the semiconductor substrate including these semiconductor elements formed thereon is collectively referred to as " chip".
[0017] Subsequently, in the photolithography process on the SiO 2 ...
PUM
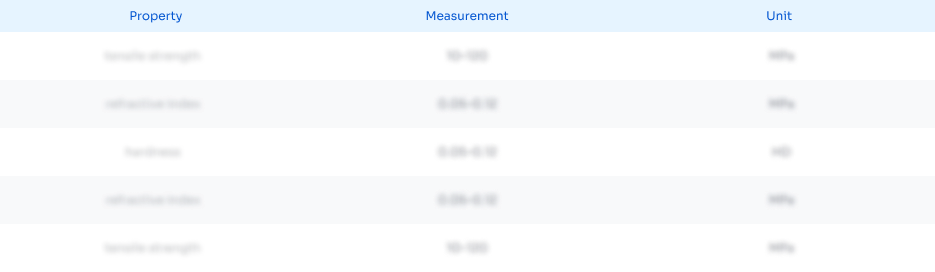
Abstract
Description
Claims
Application Information

- R&D Engineer
- R&D Manager
- IP Professional
- Industry Leading Data Capabilities
- Powerful AI technology
- Patent DNA Extraction
Browse by: Latest US Patents, China's latest patents, Technical Efficacy Thesaurus, Application Domain, Technology Topic, Popular Technical Reports.
© 2024 PatSnap. All rights reserved.Legal|Privacy policy|Modern Slavery Act Transparency Statement|Sitemap|About US| Contact US: help@patsnap.com