Oxide film forming method
A technology of oxide film and oxidation method, which is applied in the direction of electrical components, semiconductor/solid-state device manufacturing, circuits, etc., can solve the problems of uneven film thickness, difficult modification, low reliability of oxide film, etc., and achieve high-quality results
- Summary
- Abstract
- Description
- Claims
- Application Information
AI Technical Summary
Problems solved by technology
Method used
Image
Examples
Embodiment
[0126] Hereinafter, examples of the present invention will be described, but the present invention is not limited thereto.
[0127] Basically using the figure 1 The oxidation treatment device of the shown structure, according to image 3 The sequence chart shown implements the following steps.
[0128] [Pre-cleaning process]
[0129] An overetching treatment of 30% of the film thickness of the sacrificial oxide film on a silicon wafer having a diameter of 8 inches was performed in an aqueous hydrofluoric acid solution having a concentration of 1 vol % at a temperature of 23°C.
[0130] [Pre-treatment process]
[0131] (1) Loading operation
[0132] The 100 wafers obtained in the pre-cleaning process were held on a quartz wafer boat 15, placed on the cover 14, and nitrogen gas was supplied to the reaction processing chamber PC at a ratio of 19.8 slm of nitrogen and 0.2 slm of oxygen. and oxygen, the temperature in the reaction processing chamber PC is controlled at 300°C a...
PUM
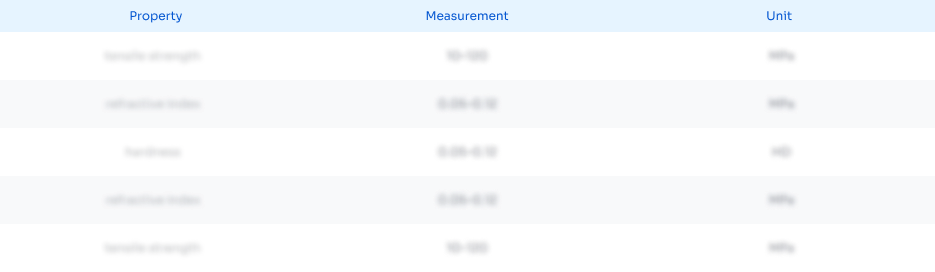
Abstract
Description
Claims
Application Information

- Generate Ideas
- Intellectual Property
- Life Sciences
- Materials
- Tech Scout
- Unparalleled Data Quality
- Higher Quality Content
- 60% Fewer Hallucinations
Browse by: Latest US Patents, China's latest patents, Technical Efficacy Thesaurus, Application Domain, Technology Topic, Popular Technical Reports.
© 2025 PatSnap. All rights reserved.Legal|Privacy policy|Modern Slavery Act Transparency Statement|Sitemap|About US| Contact US: help@patsnap.com