Method for preparing iron oxide pigment
A technology of iron oxide pigments and pigments, which is applied in the surface treatment of iron oxide pigments and the production of iron oxide pigments. It can solve the problems of difficult source of surface treatment agents, poor dispersion and suspension, and fast sedimentation speed, so as to reduce the application cost. , the effect of slowing down the settling speed and improving the dispersion
- Summary
- Abstract
- Description
- Claims
- Application Information
AI Technical Summary
Problems solved by technology
Method used
Examples
Embodiment 1
[0019] Adding 0.8 kg of sodium silicate and 0.3 kg of butyl titanate to 100 kg of slurry with an iron oxide content of 60 wt%, stirred for 1 hour, dried until the water content was less than 1 wt%, and pulverized to obtain a dry material;
[0020] Add 0.4 kg of propylene glycol and 0.4 kg of butanediol into 100 kg of the above-mentioned powder, and stir evenly to obtain the iron oxide pigment of the present invention. The test results are shown in Table 1.
Embodiment 2
[0022] Add 0.5 kg of sodium silicate and 0.1 butyl titanate to 100 kg of slurry with iron oxide content of 30 wt%, stir for 1 hour, dry the water content to less than 1 wt%, and pulverize to obtain a dry material;
[0023] Add 0.3 kg of propylene glycol and 0.3 kg of butanediol into 100 kg of the above-mentioned powder, and stir evenly to obtain the iron oxide pigment of the present invention. The test results are shown in Table 1.
Embodiment 3
[0025] Adding 0.5 kg of sodium silicate and 0.5 kg of butyl titanate to 100 kg of slurry with an iron oxide content of 30 wt%, stirring for 1 hour, until the dry water content is less than 1 wt%, pulverizing to obtain a dry material;
[0026] Add 0.3 kg of propylene glycol and 0.5 kg of butanediol into 100 kg of the above-mentioned powder, and stir evenly to obtain the iron oxide pigment of the present invention. The test results are shown in Table 1.
PUM
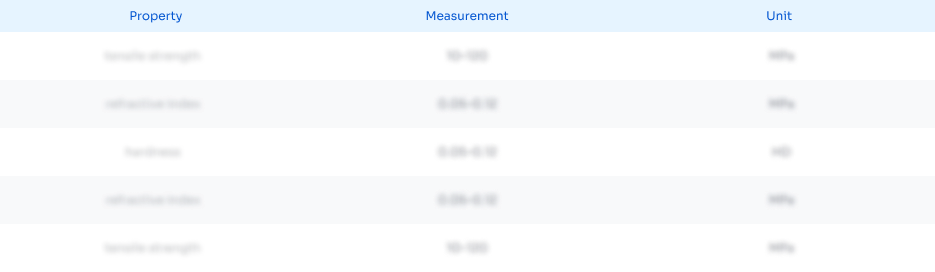
Abstract
Description
Claims
Application Information

- R&D Engineer
- R&D Manager
- IP Professional
- Industry Leading Data Capabilities
- Powerful AI technology
- Patent DNA Extraction
Browse by: Latest US Patents, China's latest patents, Technical Efficacy Thesaurus, Application Domain, Technology Topic, Popular Technical Reports.
© 2024 PatSnap. All rights reserved.Legal|Privacy policy|Modern Slavery Act Transparency Statement|Sitemap|About US| Contact US: help@patsnap.com