Blast furnace iron-making technique with hydrogen-rich fuel gas, pure oxygen and thus high efficiency and low CO2 exhaust
A blast furnace ironmaking and CO2 technology, applied in blast furnaces, blast furnace details, furnaces, etc., can solve problems such as difficult to effectively reduce the carbon dioxide emissions of blast furnaces, achieve good resource utilization compatibility, increase blast furnace utilization coefficient, and sufficient gas volume Effect
- Summary
- Abstract
- Description
- Claims
- Application Information
AI Technical Summary
Problems solved by technology
Method used
Image
Examples
Embodiment 1
[0039] at a certain 350m 3 The tuyere of the blast furnace injects natural gas and pulverized coal, and blows in pure oxygen. The production index is:
[0040] Natural gas injection volume: 800m 3 / ton of iron (ie 574kg / ton of iron)
[0041] Coke ratio: 220kg / ton of iron
[0042] Coal ratio: 154kg / ton of iron
[0043] Consumption of pure oxygen: 612m 3 / ton of iron (ie 874kg / ton of iron)
[0044] Bosh gas composition: H 2 : 57%; CO: 43%
[0045] Theoretical combustion temperature: 2006°C
[0046] Furnace top gas composition: CO: 37%; CO 2 : 10.2%; H 2 : 52.5%; N 2 : 0.26%; S: 0.05%
[0047]Furnace top gas volume: 2607m 3 / ton of iron (equivalent to 1869kg / ton of iron)
Embodiment 2
[0049] at a certain 350m 3 The tuyere of blast furnace injects natural gas, coke oven gas and coal powder, and blows in pure oxygen. The production index is:
[0050] Natural gas injection volume: 500m 3 / ton of iron (ie 359kg / ton of iron)
[0051] Coke oven gas injection volume: 270m 3 / ton of iron (ie 103kg / ton of iron)
[0052] Coke ratio: 200kg / ton of iron
[0053] Coal ratio: 160kg / ton of iron
[0054] Consumption of pure oxygen: 500m 3 / ton of iron (ie 715kg / ton of iron)
[0055] Bosh gas composition, H 2 : 57.2%; CO: 42.8%
[0056] Theoretical combustion temperature: 2149°C
[0057] Furnace top gas composition: CO: 35.3%; CO 2 : 12.7%; H 2 : 51.6%; N 2 : 0.33%; S: 0.06%
[0058] Furnace top gas volume: 2130m 3 / ton of iron (equivalent to 1589kg / ton of iron)
PUM
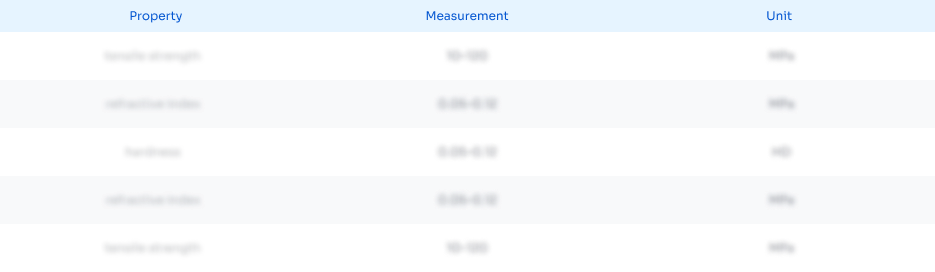
Abstract
Description
Claims
Application Information

- R&D
- Intellectual Property
- Life Sciences
- Materials
- Tech Scout
- Unparalleled Data Quality
- Higher Quality Content
- 60% Fewer Hallucinations
Browse by: Latest US Patents, China's latest patents, Technical Efficacy Thesaurus, Application Domain, Technology Topic, Popular Technical Reports.
© 2025 PatSnap. All rights reserved.Legal|Privacy policy|Modern Slavery Act Transparency Statement|Sitemap|About US| Contact US: help@patsnap.com