Etching method for anti-reflecting coating layer on organic substrate
A bottom anti-reflection and coating layer technology, which is applied in the direction of electrical components, semiconductor/solid-state device manufacturing, circuits, etc., can solve the problem that the error of the key dimension of the line width is difficult to grasp, and achieve the effect of improving accuracy
- Summary
- Abstract
- Description
- Claims
- Application Information
AI Technical Summary
Problems solved by technology
Method used
Image
Examples
Embodiment Construction
[0018] The invention provides a kind of plasma etching gas for etching the organic bottom anti-reflection coating layer, which is to partially replace the halothane gas (C x h y f z ) as the main etching gas, because part of the replacement of halothane gas can generate halothane polymer on the sidewall of the photoresist pattern to protect the sidewall of the photoresist pattern from lateral etching, so that the gap between the patterns will not become larger and affect the etching critical size. The auxiliary gases used include chlorine, nitrogen, partially substituted halothane gases (for example: methane fluoride (CH 3 F), difluoromethane (CH 2 f 2 ) etc.) or fully substituted fluorine gas (for example: carbon tetrafluoride (CF 4 ), carbon hexafluoride (C 2 f 6 ), three carbon octafluoride (C 3 f 8 ) or tetracarbon octafluoride (C 4 f 8 )Wait).
[0019] Figure 1A to Figure 1B It is a cross-sectional view of a process for etching an organic bottom anti-reflecti...
PUM
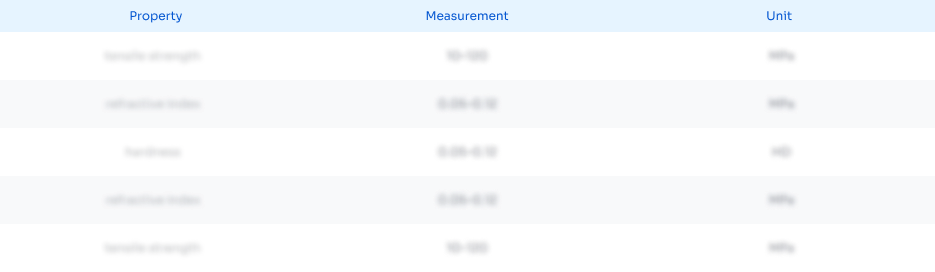
Abstract
Description
Claims
Application Information

- Generate Ideas
- Intellectual Property
- Life Sciences
- Materials
- Tech Scout
- Unparalleled Data Quality
- Higher Quality Content
- 60% Fewer Hallucinations
Browse by: Latest US Patents, China's latest patents, Technical Efficacy Thesaurus, Application Domain, Technology Topic, Popular Technical Reports.
© 2025 PatSnap. All rights reserved.Legal|Privacy policy|Modern Slavery Act Transparency Statement|Sitemap|About US| Contact US: help@patsnap.com