Damascene process for chemically vapor depositing titanium nitride and copper metal layer
A chemical vapor phase, copper metal technology, applied in the direction of electrical components, semiconductor/solid-state device manufacturing, circuits, etc., can solve the problems of low deposition rate and poor quality, and achieve low process stability, simple process, and good adhesion Effect
- Summary
- Abstract
- Description
- Claims
- Application Information
AI Technical Summary
Problems solved by technology
Method used
Examples
Embodiment Construction
[0020] 1. Using He 2 Carrying Ti-containing chemical substance TDMA, under the condition of low vacuum 1.5Torr, TiN film is deposited by thermal decomposition. Deposition temperature is 450C, deposition time is 15 seconds, TDMAT flow rate is 225sccm, He 2 The flow rate is 275sccm, N 2 The flow rate is 300sccm.
[0021] 2. In situ H 2 -N 2Radio frequency plasma treatment reduces the content of impurities such as carbon, oxygen, and hydrogen in the CVD-deposited TiN film, reduces the resistivity, makes the TiN grain grow uniformly, densifies the TiN film, and improves the uniformity of film thickness. The processing vacuum is 1.5 Torr, and the time is 35 seconds.
[0022] 3. Processes 1 and 2 are used cyclically to deposit 35 nm of TiN barrier material.
[0023] 4. Chemical vapor deposition of Cu metal film: using Cu-containing organic Cu I (hafc)(vtms) thermally decomposes at a temperature of 180°C and a vacuum of 1-3 Torr to form a pure Cu film. The chemical reaction fo...
PUM
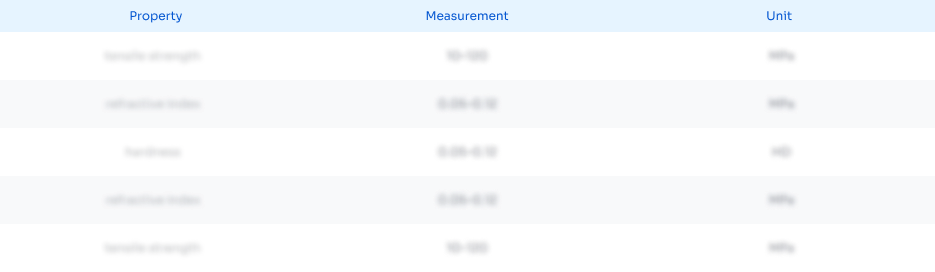
Abstract
Description
Claims
Application Information

- R&D
- Intellectual Property
- Life Sciences
- Materials
- Tech Scout
- Unparalleled Data Quality
- Higher Quality Content
- 60% Fewer Hallucinations
Browse by: Latest US Patents, China's latest patents, Technical Efficacy Thesaurus, Application Domain, Technology Topic, Popular Technical Reports.
© 2025 PatSnap. All rights reserved.Legal|Privacy policy|Modern Slavery Act Transparency Statement|Sitemap|About US| Contact US: help@patsnap.com