Multilayer nickel-iron alloy composite coating process
An iron alloy and multi-layer nickel technology, which is applied in the field of multi-layer nickel-iron alloy composite coating process, can solve the problems of complex electroplating process, coating thickness, poor hardness and corrosion resistance, etc., and achieve simple coating process and bright and smooth coating surface , the effect of high hardness
- Summary
- Abstract
- Description
- Claims
- Application Information
AI Technical Summary
Problems solved by technology
Method used
Examples
Embodiment Construction
[0008] 1. Use sodium carbonate cleaning solution to degrease the metal surface, and use 31% hydrochloric acid to derust the plated metal surface;
[0009] 2. Weigh nickel chloride, sodium acetate, nickel sulfate, ferrous sulfate, and ferric chloride to be 60 grams, 60 grams, 250 grams, 10 grams, and 10 grams, respectively, and dissolve them in one liter of water. Add 25 grams of boric acid in the solution to obtain solution (A).
[0010] 3. Get 250 grams of nickel sulfamate and 60 grams of nickel chloride and dissolve them in one liter of water, then add boric acid until the solution is in a saturated state to obtain solution (B);
[0011] 4. Fully mix the solution (A) and the solution (B) to prepare the mixed solution (C), and the pH value of the mixed solution (C) is 3.5.
[0012] 5. Apply the solution (A), solution (B) and mixed solution (C) evenly on the surface of the coating in sequence with a coater. The working current of the coater is 0.5-30A, and the working voltage...
PUM
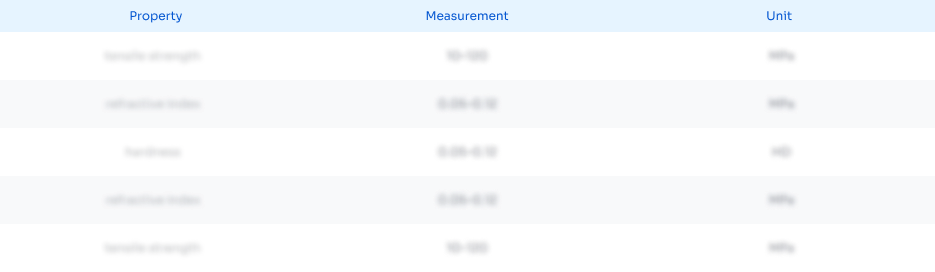
Abstract
Description
Claims
Application Information

- Generate Ideas
- Intellectual Property
- Life Sciences
- Materials
- Tech Scout
- Unparalleled Data Quality
- Higher Quality Content
- 60% Fewer Hallucinations
Browse by: Latest US Patents, China's latest patents, Technical Efficacy Thesaurus, Application Domain, Technology Topic, Popular Technical Reports.
© 2025 PatSnap. All rights reserved.Legal|Privacy policy|Modern Slavery Act Transparency Statement|Sitemap|About US| Contact US: help@patsnap.com