Polyacrylonitrile-radical hollow carbon-fiber film and preparing method thereof
A polyacrylonitrile-based, carbon fiber membrane technology, applied in the field of membrane separation
- Summary
- Abstract
- Description
- Claims
- Application Information
AI Technical Summary
Problems solved by technology
Method used
Examples
Embodiment 1
[0021] (1) Preparation process of casting solution: choose dimethylacetamide as solvent, add polyacrylonitrile, its weight ratio to dimethylacetamide is 12:88 (that is, PAN concentration is 12%), then add polymethyl acetamide Methyl acrylate, polyvinylpyrrolidone; polyacrylonitrile, polymethyl methacrylate, and polyvinylpyrrolidone with a weight percentage of 80:10:10, dissolved at 70°C to form a homogeneous casting solution;
[0022] (2) Spinning process: Spin the hollow fiber membrane with the cast membrane solution, water is the coagulation bath, and the spinning temperature is 45°C;
[0023] (3) stretching process: after the spinning process, the hollow fiber membrane spun is stretched, the rotating speed of the godet roller is adjusted, and the stretching ratio is controlled to be 1;
[0024] (4) Post-treatment process: soak the spun hollow fiber membrane for 24 hours with 40% glycerin aqueous solution by weight, then take it out and dry it, and carry out dehydration trea...
Embodiment 2
[0029] (1) Casting solution preparation process: the concentration ratio of PAN in the casting solution is 14.5:85.5; polyimide is added; the weight ratio of polyacrylonitrile, polymethyl methacrylate, polyimide, and polyvinylpyrrolidone is 75: 5: 10: 10, the rest is the same as in Example 1;
[0030] (2) spinning process: with embodiment 1;
[0031] (3) Stretching process: the control draw ratio is 1.5 times, the rest is the same as embodiment 1;
[0032] (4) post-treatment process: with embodiment 1;
[0033] (5) Pre-oxidation process: the heating rate is 5°C / min, the temperature rises from 25°C to 250°C, and is kept for 1 hour; the remainder is the same as in Example 1
[0034] (7) Carbonization process: heat up to 850°C, the heating rate is 10°C / min, keep warm for 1.5 hours, the same as
[0035] Example 1.
[0036] It has been determined that the polyacrylonitrile-based hollow carbon fiber membrane of the present invention has a molecular weight cut-off of 100,000, a p...
Embodiment 3
[0038] (1) Casting solution preparation process: PAN, PMMA, PI, PVP weight percent is 70: 5: 15: 10; PAN concentration ratio is 18: 82, the remainder is the same as embodiment 2;
[0039] (2) spinning process: with embodiment 1;
[0040] (3) stretching process: the control stretching ratio is 3, the rest is the same as embodiment 1;
[0041] (4) post-treatment process: with embodiment 1;
[0042] (5) Pre-oxidation process: the heating rate is 8°C / min, the temperature rises from 25°C to 300°C, and the temperature is kept for 0.5 hours, the remainder is the same as in Example 1;
[0043] (6) Carbonization process: the temperature was raised to 750° C., the heating rate was 10° C. / min, and the temperature was kept for 3 hours. The remainder was the same as in Example 2.
[0044] It has been determined that the polyacrylonitrile-based hollow carbon fiber membrane of the present invention has a molecular weight cut-off of 150,000, a porosity of 60%, and a flux of 160 l / m at an op...
PUM
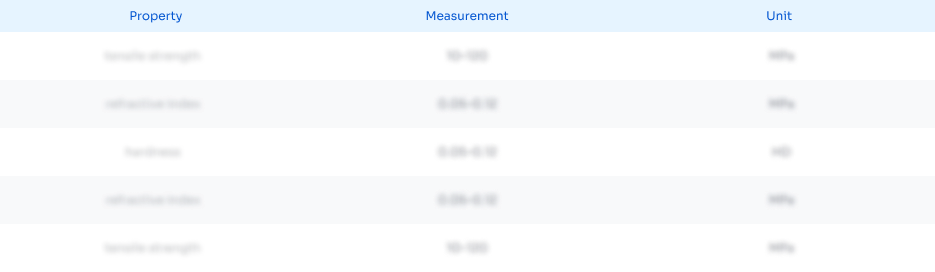
Abstract
Description
Claims
Application Information

- R&D Engineer
- R&D Manager
- IP Professional
- Industry Leading Data Capabilities
- Powerful AI technology
- Patent DNA Extraction
Browse by: Latest US Patents, China's latest patents, Technical Efficacy Thesaurus, Application Domain, Technology Topic, Popular Technical Reports.
© 2024 PatSnap. All rights reserved.Legal|Privacy policy|Modern Slavery Act Transparency Statement|Sitemap|About US| Contact US: help@patsnap.com