Method for mfg. parallel capacitor core, and parallel capacitor core
A manufacturing method and capacitor technology, applied in the direction of capacitor manufacturing, capacitors, multiple fixed capacitors, etc., can solve the problems of capacitor breakdown, overheating of surrounding media, low dielectric strength, etc., to improve partial discharge performance, avoid melting and Shrinkage and the effect of ensuring compressive strength
- Summary
- Abstract
- Description
- Claims
- Application Information
AI Technical Summary
Problems solved by technology
Method used
Image
Examples
Embodiment 1
[0020] As shown in the figure, take the aluminum foil 8 and the polypropylene film 9 and place them on the rolling machine for rolling; assemble the rolled components 2 into a core group; place the core group on the workbench, and set the Parallel connection, welding is performed on the upper end surface of the core group along the vertical direction of the side of the component to form a weld bead 3; then reverse welding is performed on the upper end surface of the core group in the opposite direction to the weld bead 3 to form another weld bead 4, two weld bead 3 , 4 leave gap between; Carry out welding with the same method at the lower end face of core group, also form weld bead 3,4, weld lead wire 7 respectively on weld bead 3,4, make capacitor core after packing with cable paper 1.
Embodiment 2
[0022] As shown in the figure, take the aluminum foil 8 and the polypropylene film 9 and place them on the rolling machine for rolling; assemble the rolled components 2 into a core group; place the core group on the workbench, and set the Parallel relationship, weld the upper end face of the core group along the direction of the vertical component side to form a weld bead 3, and bury the metal connecting piece 5 on the weld bead 3 to prevent the weld bead 3 from breaking; 3 Weld the opposite direction to perform reverse welding to form another weld bead 4, and bury the metal connecting piece 6 on the weld bead 4 to prevent the weld bead 4 from breaking, and leave a gap between the two weld bead 3, 4; The lower end face of the group is welded with the same welding method to form another two weld beads 3, 4, and metal connecting pieces 5, 6 are also buried and welded on the weld beads 3, 4; the weld beads 3, 6 on the upper and lower end faces of the core group 4 Solder the lead ...
Embodiment 3
[0024] The shunt capacitor core has a core group consisting of several elements 2, said elements 2 are made of aluminum foil 8 and polypropylene film 9 rolled together, and there are two welding beads 3 and 3 on the upper and lower end faces of the core group respectively. 4. The welding directions of the welding beads 3 and 4 are opposite, and there is a gap between the welding beads 3 and 4, the aluminum foil 8 and the polypropylene film 9 near the welding beads 3 and 4 are twisted, and the twisting direction is opposite , lead wires 7 are respectively welded on the weld beads 3 and 4, and cable paper 1 is wrapped on the surface of the core group.
PUM
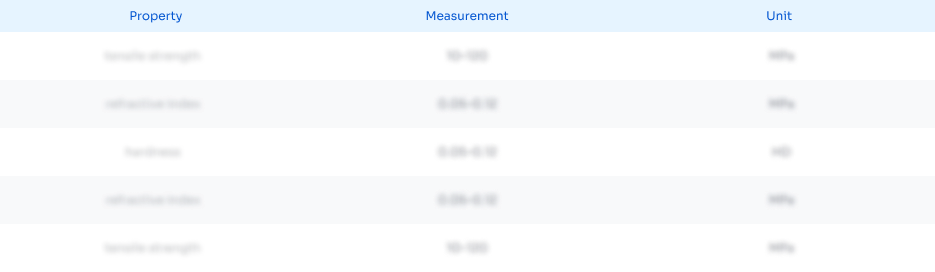
Abstract
Description
Claims
Application Information

- R&D
- Intellectual Property
- Life Sciences
- Materials
- Tech Scout
- Unparalleled Data Quality
- Higher Quality Content
- 60% Fewer Hallucinations
Browse by: Latest US Patents, China's latest patents, Technical Efficacy Thesaurus, Application Domain, Technology Topic, Popular Technical Reports.
© 2025 PatSnap. All rights reserved.Legal|Privacy policy|Modern Slavery Act Transparency Statement|Sitemap|About US| Contact US: help@patsnap.com