Process for preparing bromodifluoacetic acid compounds
A technology of bromodifluoroacetic acid and bromodifluoroacetyl halide, which is applied in the field of preparation of alkyl bromodifluoroacetate
- Summary
- Abstract
- Description
- Claims
- Application Information
AI Technical Summary
Problems solved by technology
Method used
Examples
Embodiment Embodiment 1
[0053] Example Example 1: From 1.2-dibromo-1.1-difluoro-2.2-dichloroethane CF 2 BrCCl 2 Br Preparation of ethyl bromodifluoroacetate Esters (BDFAE) a) CF 2 BrCCl 2 Preparation of Br - Reaction:
[0054] F122 F1112a
[0055] - Preparation of 1,1-difluoro-2,2-dichloroethylene (F1112a):
[0056] 508.5 g (3 mol) of F122 and 2 g of Noramium M2C (dicocodimethylammonium chloride) were charged into a 1 liter Sovirel-type glass reactor, which was pre-dried and nitrogen-filled, equipped with mechanical stirring , isobaric dropping funnel and distillation column, the distillation column is equipped with a device that can adjust the reflux rate. The reaction medium is heated to 50° C. to 70° C., and then 439 g (3.3 mol) of a 10N sodium hydroxide solution are poured in within 3 hours. As the reaction proceeded, F1112a was distilled and reconcentrated in a dry ice-cooled trap.
[0057] After the reaction, the conversion rate of F122 was 97%, while the yield of F...
Embodiment 2
[0087] δ(CH 3 ) = 1.40ppm Example 2: Depend on CF 2 BrCCl 2 Br Preparation of bromodifluoroacetic acid:
[0088] 153g (0.5mol) of 1,2-dibromo-1,1-difluoro-2,2-dichloroethane prepared earlier was loaded into 500cm 3 In the first glass reactor, the reactor was equipped with mechanical stirring, an isobaric dropping funnel and a distillation column topped with a timer to adjust the reflux rate.
[0089] The drain of the distillation column was connected to a second reactor containing 150 g of water. The reactor was jacketed (5° C.) cooled and equipped with mechanical stirring and a condenser connected to a water absorber.
[0090] Heat the reagents in the first reactor to 50 °C, then pour 123 g of 65% oleum, equivalent to 1 mole of SO, over 2 hours and 30 minutes 3 . The continuously withdrawn distillation fraction containing bromodifluoroacetyl halides is hydrolyzed in a second reactor maintained at a temperature of about 25°C. After the reaction was complete, the a...
Embodiment 3
[0091] A 7% sodium sulfite solution was added to the contents of the second reactor to remove traces of bromine. Bromodifluoroacetic acid was then extracted with isopropyl ether, followed by distillation under reduced pressure. The yield of bromodifluoroacetic acid calculated as the perhalogenated derivative was 80%. Example 3: From 1,1-difluorotetrabromoethane CF 2 BrCBr 3 Preparation of ethyl bromodifluoroacetate (BDFAE)
[0092] a) through 1,1-difluoro-1,2-dibromoethane CF 2 BrCH 2 Preparation of CF by Thermal Bromination of Br 2 BrCBr 3 :
[0093] Bromination was carried out in the gas phase in a vertically placed and electric oven heated quartz tube (2.2 cm in diameter and 39 cm in length). Add 0.12mol / h CF continuously at the top of the tube simultaneously 2 BrCH 2 Br and 0.30 mol / h bromine. After a residence time of 20 seconds in the tube at 520°C, the vapor from the bottom of the test tube was condensed by a double loop condenser (-10°C) and...
PUM
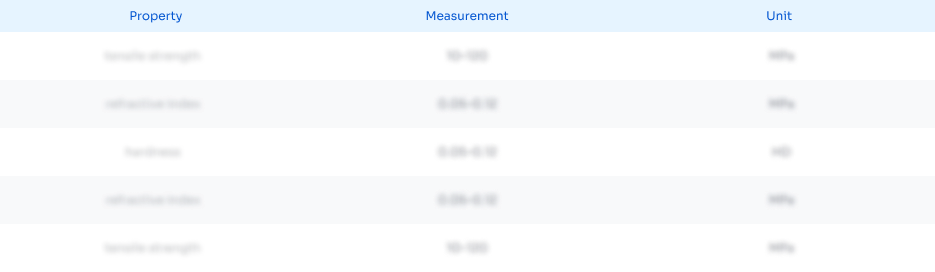
Abstract
Description
Claims
Application Information

- Generate Ideas
- Intellectual Property
- Life Sciences
- Materials
- Tech Scout
- Unparalleled Data Quality
- Higher Quality Content
- 60% Fewer Hallucinations
Browse by: Latest US Patents, China's latest patents, Technical Efficacy Thesaurus, Application Domain, Technology Topic, Popular Technical Reports.
© 2025 PatSnap. All rights reserved.Legal|Privacy policy|Modern Slavery Act Transparency Statement|Sitemap|About US| Contact US: help@patsnap.com