Process for preparing calcium magnesium acetate by vacuum distillation method
A technology of calcium magnesium acetate and distillation method, which is applied in the preparation of carboxylate, organic chemistry, etc., can solve the problems of large volatilization loss of acetic acid, decrease of product purity, high temperature requirements, etc., and achieve product purity improvement, simple dehydration, and reaction The effect of low temperature
- Summary
- Abstract
- Description
- Claims
- Application Information
AI Technical Summary
Problems solved by technology
Method used
Image
Examples
Embodiment 1
[0013] Take 500ml of deionized water at room temperature, slowly add 2.878mol of glacial acetic acid, then add 0.483mol of CaO and 1.100mol of MgO at one time, and stir to make it react for 1.5hr, the solution is slightly yellow, and the reaction temperature is 45±5℃. Adjust the pH value with a calcium-magnesium mixture with a molar ratio of Ca:Mg=3:7 until the solution shows weak alkaline pH=7.4, centrifuge and filter to separate excess calcium and magnesium oxide after resting. The pH of the mother liquor was measured to be 9.11.
[0014] Put the mother liquor into a rotary evaporator and carry out vacuum distillation at a pressure of -0.096 to -0.098MPa and a temperature of 50±5°C. After vacuum distillation for 1.5 hours, a large amount of white crystals precipitated, and the volume of the distillate was measured. The distillate was measured by high pressure liquid chromatography, and the concentration of acetate ion was 2.475×10 -3 mol / L, pH=4.60, the loss rate of acetic ...
Embodiment 2
[0016] Take 500ml of deionized water at room temperature, slowly add 4.029mol of glacial acetic acid, then add 0.672mol of CaO and 1.34mol of MgO at one time, and stir to make it react for 2 hours. The solution is slightly yellow, and the reaction temperature is 70±5℃. The calcium and magnesium mixture with a molar ratio of Ca:Mg=3:6 is used to adjust the pH value until the solution shows a weakly alkaline pH=8.5. After resting, centrifuge and filter to separate excess calcium and magnesium oxide. The pH of the mother liquor was measured to be 9.56.
[0017] Put the mother liquor into a rotary evaporator and carry out vacuum distillation at a pressure of -0.095 to -0.098 MPa and a temperature of 75±5°C. After 3.5 hours of vacuum distillation, a large amount of white crystals precipitated, and the volume of the distillate was measured. The distillate was measured by high pressure liquid chromatography, and the concentration of acetate ion was 3.755×10 -3 mol / L, pH=4.16, the lo...
Embodiment 3
[0019] Take 500ml of deionized water at room temperature, add 0.483mol of CaO and 1.100mol of MgO to form a mixed emulsion of calcium oxide and magnesium oxide, slowly add 2.878mol of glacial acetic acid, and stir to make it happen. Control the temperature at 85±5 Between ℃, the required time of complete reaction is about 3 hours, and the obtained mother liquor is similar to Example 1.
[0020] Put the mother liquor into a rotary evaporator and carry out vacuum distillation. The control pressure is -0.083~-0.086Mpa, and the other conditions are the same. The required temperature for vacuum distillation is 85±5°C and the required time is 5hr. The concentration of acetate ion in the distillate is 6.635×10 -3 mol / L, pH=3.62, acetic acid loss rate is 0.015%.
PUM
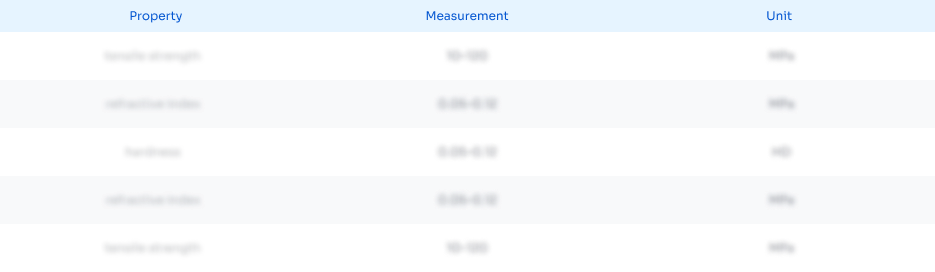
Abstract
Description
Claims
Application Information

- Generate Ideas
- Intellectual Property
- Life Sciences
- Materials
- Tech Scout
- Unparalleled Data Quality
- Higher Quality Content
- 60% Fewer Hallucinations
Browse by: Latest US Patents, China's latest patents, Technical Efficacy Thesaurus, Application Domain, Technology Topic, Popular Technical Reports.
© 2025 PatSnap. All rights reserved.Legal|Privacy policy|Modern Slavery Act Transparency Statement|Sitemap|About US| Contact US: help@patsnap.com