Polymerizing process for preparing nano microcapsule by radiating emulsion
A technology of nano-microcapsules and emulsion polymerization, which is applied in the field of preparation of nano-microcapsules by radiation emulsion polymerization, which can solve the problems of difficult control of the reaction process, small molecular weight of polymers, and many condensed slags, and achieve simple equipment and production processes, high polymerization Molecular weight and low cost effect
- Summary
- Abstract
- Description
- Claims
- Application Information
AI Technical Summary
Problems solved by technology
Method used
Examples
Embodiment 1
[0021] 1. Weigh the raw materials according to the composition ratio: oily capsule core 40Kg (accounting for 40% of the total mass of the system), monomeric styrene 10Kg, monomeric acrylonitrile 5Kg (the total mass of monomers accounts for 15% of the total mass of the system), emulsified Agent alkylphenol polyoxyethylene ether 2Kg, emulsifier Pingjia 1Kg (the total mass of the emulsifier accounts for 3% of the total mass of the system), and 42Kg of water (accounting for 42% of the total mass of the system) for subsequent use;
[0022] Put the weighed oily capsule core, monomer butyl acrylate, styrene, and acrylonitrile into a container and mix evenly, then add the weighed emulsifier alkylphenol polyoxyethylene ether, Pingajia, and water into the container;
[0023] 2. Put the stirrer with a homogenizer into the above container, start the stirring motor, adjust the speed, from slow to fast, and stir vigorously for 15-45 minutes;
[0024] 3. Put the contents of the above contain...
Embodiment 2
[0030] 1. Weigh the raw materials according to the composition ratio: oily capsule core 10Kg (accounting for 10% of the total mass of the system), monomer methyl methacrylate 15Kg, monomer styrene 20Kg, monomer acrylic acid 0.5Kg monomer butyl acrylate 4.5 Kg (the total mass of the monomer accounts for 40% of the total mass of the system), 5Kg of the emulsifier alkylphenol polyoxyethylene ether, 5Kg of the emulsifier Pingjia (the total mass of the emulsifier accounts for 10% of the total mass of the system), 40Kg of water (accounts for 40% of the total mass of the system) for standby;
[0031] Put the weighed oily capsule core, monomer methyl methacrylate, styrene, acrylic acid, and butyl acrylate into a container and mix evenly, then add the weighed emulsifier alkylphenol polyoxyethylene ether, Pingajia, Water is added to the container;
[0032] 2. Put the stirrer with a homogenizer into the above container, start the stirring motor, adjust the speed, from slow to fast, and ...
Embodiment 3
[0039] 1. Weigh the raw materials according to the composition ratio: oily capsule core 2Kg (accounting for 2% of the system mass), monomer butyl acrylate 1Kg, monomer styrene 3Kg, monomer acrylonitrile 1Kg (the total mass of the monomer accounts for the total mass of the system) 5%), emulsifier fatty alcohol sulfate 1Kg (emulsifier accounts for 1% of the total system mass), water 92Kg (accounts for 92% of the system total mass) for subsequent use;
[0040] Put the weighed oily capsule core, monomer butyl acrylate, styrene, and acrylonitrile into a container and mix evenly, then add the weighed emulsifier fatty alcohol sulfate salt and water into the container;
[0041] 2. Put the stirrer with homogenizer into the above container, start the stirring motor, adjust the speed, from slow to fast, stir vigorously for 15-20 minutes;
[0042] 3. Put the contents of the above container into a reaction kettle with stirring device, jacket cooling or spraying device, and put the reaction...
PUM
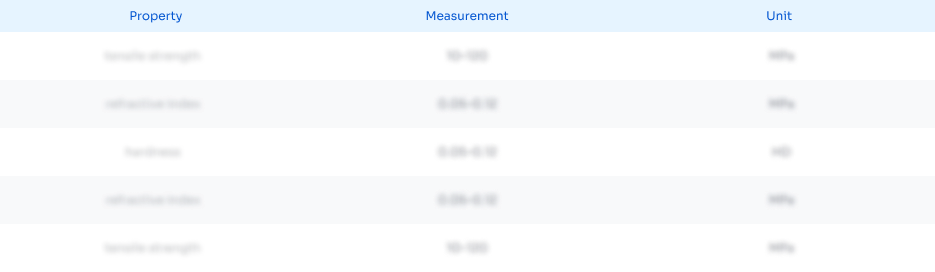
Abstract
Description
Claims
Application Information

- R&D Engineer
- R&D Manager
- IP Professional
- Industry Leading Data Capabilities
- Powerful AI technology
- Patent DNA Extraction
Browse by: Latest US Patents, China's latest patents, Technical Efficacy Thesaurus, Application Domain, Technology Topic, Popular Technical Reports.
© 2024 PatSnap. All rights reserved.Legal|Privacy policy|Modern Slavery Act Transparency Statement|Sitemap|About US| Contact US: help@patsnap.com