Ablative material of resin of phenolic cyanate
A technology of phenolic cyanate ester and ablation material, applied in the field of high temperature resistant ablation material, can solve the problems of high melt viscosity, high heteroatom content, low carbon content and the like
- Summary
- Abstract
- Description
- Claims
- Application Information
AI Technical Summary
Problems solved by technology
Method used
Image
Examples
Embodiment 1
[0026] Example 1: Synthesis of novolac cyanate
[0027] The 37% aqueous solution of phenol and formaldehyde and the molar ratio of oxalic acid are 1:0.9:0.005, put into a three-necked flask equipped with a reflux condenser, react at 80~100℃ for 3~5 hours, wash with water and vacuum to obtain the softening point Novolac and novolac are dissolved in a mixed solvent of dichloromethane and ethyl acetate at 40~60℃, put into a four-neck flask with BrCN, dropwise add triethylamine, phenolic hydroxyl group, BrCN and triethylamine The molar ratio of is 1:1.05:1.10, the reaction is conducted at -15°C to -5°C for 5 hours, the salt and the solvent are separated, and the purification process is performed to obtain the novolac cyanate. In this case, n=2~5, m=0.
[0028] 1-2: Using the same method as 1-1, change the phenol to p-phenylphenol to obtain the novolac cyanate. In this case, n=2~5, m=0.
[0029] 1-3: Using the same method as 1-1, change the phenol to o-phenylphenol to obtain the novola...
Embodiment 2
[0030] 1-4: Reacting phenol and p-phenylphenol with benzaldehyde and p-toluenesulfonic acid at a molar ratio of 1:1:1.5:0.01, and then using the same method as 1-1 to obtain novolac cyanate. In this case, n=2~5, m=0. Example 2: Synthesis of linear fused ring phenol cyanate
[0031] 2-1: 1-Naphthol and formaldehyde 37% aqueous solution and oxalic acid molar ratio 1:0.80:0.005, put into a three-necked flask equipped with reflux condenser, in the presence of ketone solvent, at 60-100 ℃ React for 3 to 5 hours, wash with water, and vacuum to obtain a linear fused-ring phenol phenol with a softening point of 40-60°C. The linear fused-ring phenolic aldehyde is dissolved in dichloromethane solvent, put into a four-necked flask with BrCN, and triethylamine is added dropwise. The molar ratio of phenolic hydroxyl group to BrCN and triethylamine is 1:1.05:1.10, at -15℃~ React at -5°C for 5 hours, separate the salt and solvent, and perform purification treatment to obtain linear fused-ring phe...
Embodiment 3
[0034] Example 3: Synthesis of copolymerized phenolic cyanate
[0035] 3-1: A 37% aqueous solution of phenol, naphthol (molar ratio 1:1) and formaldehyde, and oxalic acid in a phenol, aldehyde, acid molar ratio of 1:0.9:0.005, put them into a three-necked flask equipped with a reflux condenser, React at 80~100℃ for 3~5 hours, wash with water and vacuum to obtain copolymerized phenolic aldehyde. The copolymerized phenolic aldehyde is dissolved in acetone solvent and put into a four-necked flask together with BrCN. Triethylamine, phenolic hydroxyl and BrCN are added dropwise. The molar ratio of the triethylamine is 1:1.05:1.10, and the reaction is carried out at -15°C to -5°C for 5 hours, the salt and the solvent are separated, and the purification treatment is performed to obtain the copolymerized phenol aldehyde cyanate. In this case, n:m=1:1.
[0036] 3-2: Change the molar ratio of phenol and naphthol to 1:2, and obtain the copolymerized phenol cyanate in the same way as benzalde...
PUM
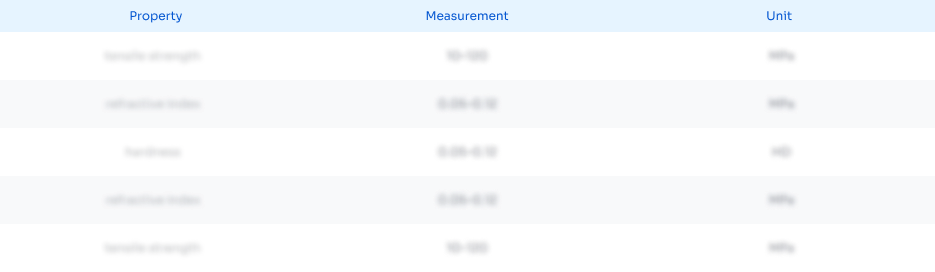
Abstract
Description
Claims
Application Information

- R&D
- Intellectual Property
- Life Sciences
- Materials
- Tech Scout
- Unparalleled Data Quality
- Higher Quality Content
- 60% Fewer Hallucinations
Browse by: Latest US Patents, China's latest patents, Technical Efficacy Thesaurus, Application Domain, Technology Topic, Popular Technical Reports.
© 2025 PatSnap. All rights reserved.Legal|Privacy policy|Modern Slavery Act Transparency Statement|Sitemap|About US| Contact US: help@patsnap.com