Zinc-impregnating layer anodic oxidation method colouring process and its treatment solution formula
An anodizing method and a technology for treating solutions, which are applied in the coating process of metal materials, coating, and plating of superimposed layers, etc., can solve problems such as environmental pollution, achieve no environmental pollution, solve environmental pollution problems, and have good stability. Effect
- Summary
- Abstract
- Description
- Claims
- Application Information
AI Technical Summary
Problems solved by technology
Method used
Examples
Embodiment 1
[0021] First add 3 / 4 of distilled water into the 5L tank, add 150g potassium hydroxide, 150g potassium oxalate and 200g aniline in sequence, then add water to the predetermined volume, and after the treatment solution is left for 24 hours, remove the AZ91 magnesium alloy parts as the anode. Oil and water washing, pickling, water washing, alkali washing, activation, water washing, zinc immersion, water washing, and then at 10°C, with AZ91 magnesium alloy zinc dipped parts as anode and stainless steel as cathode, pass through the treatment solution with The frequency is 500Hz, the on-off ratio is 5%, and the current density is 0.5A / dm 2 After anodizing for 1 minute, cut off the power, rinse with tap water, and dry with hot air. A dense iridescent film layer can be obtained.
Embodiment 2
[0023] First add 3 / 4 of distilled water to the 10L tank, then add 350g potassium hydroxide, 350g potassium oxalate and 300g aniline in turn, then add water to the predetermined volume, after standing still for 24 hours, degrease and clean the LY12 aluminum alloy as the anode Rinse, pickle, rinse with water, rinse with alkali, activate, rinse with water, dip in zinc, rinse with water, then use LY12 aluminum alloy zinc dipped as anode and stainless steel as cathode at 15°C, pass through the treatment solution with a frequency of 1500Hz, The on-off ratio is 10%, and the current density is 0.3A / dm 2 After 2 minutes of anodizing, cut off the power, rinse with tap water, and dry with hot air. A dense iridescent film layer can be obtained.
Embodiment 3
[0025] Add 3 / 4 distilled water to the 5L tank, add 125g potassium hydroxide, 200g potassium oxalate and 175g aniline in sequence, then add water to the predetermined volume, after standing still for 24 hours, degrease and clean the AM60 magnesium alloy as the anode Washing, pickling, water washing, alkali washing, activation, water washing, zinc dipping, water washing, and then at 40°C, use AM60 magnesium alloy zinc dipped parts as anode and stainless steel as cathode, pass through the treatment solution with a frequency of 800Hz, On-off ratio 5%, current density 1A / dm 2 Current treatment, after anodizing for 0.5 minutes, cut off the power, rinse with tap water, and dry with hot air. A dense iridescent film layer can be obtained.
PUM
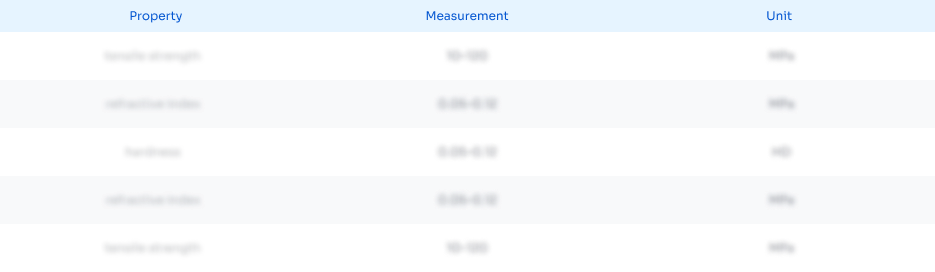
Abstract
Description
Claims
Application Information

- R&D Engineer
- R&D Manager
- IP Professional
- Industry Leading Data Capabilities
- Powerful AI technology
- Patent DNA Extraction
Browse by: Latest US Patents, China's latest patents, Technical Efficacy Thesaurus, Application Domain, Technology Topic, Popular Technical Reports.
© 2024 PatSnap. All rights reserved.Legal|Privacy policy|Modern Slavery Act Transparency Statement|Sitemap|About US| Contact US: help@patsnap.com