Process for preparing high shock-resistance polyacrylic ester composite particle grafted vinyl chloride emulsion resin
A polyacrylate and composite particle technology, which is applied in the field of preparation of high-impact polyacrylate composite particles grafted with vinyl chloride emulsion resin, can solve the problem of poor macromolecular chain fluidity, poor weather resistance of polyvinyl chloride, and low notch impact strength. And other issues
- Summary
- Abstract
- Description
- Claims
- Application Information
AI Technical Summary
Problems solved by technology
Method used
Image
Examples
Embodiment 1
[0075] (1) Preparation of polyacrylate (ACR) composite latex
[0076] Add 100ml deionized water, 0.20g sodium lauryl sulfate, 0.05g potassium persulfate (K 2 S 2 o 8 ) and seed comonomer mixture [2.86g butyl acrylate (BA), 1.54g 2-ethylhexyl acrylate (EHA), 0.066g 1,4-butanediol diacrylate (BDDA)], at room temperature Stir and blow nitrogen to make it fully emulsified. Then, add 0.15g sodium borate (Na 2 BO 4 10H 2 O) adjust the pH between 8 and 9. Start the water bath to heat up, and feed the cooling water to the reflux condenser at the same time.
[0077] When the reaction started, the system exothermicly increased in temperature. When the temperature of the reaction liquid was constant to 75°C, the reaction was kept for 1 hour. Then add 0.08g SDS and 0.10g K 2 S 2 o 8 At the same time, the mixed liquid of the core layer monomer (11.44gBA, 6.16g EHA, 0.264g BDDA) was added dropwise. After the dropwise addition of the core layer monomer mixture was completed, 0.1...
Embodiment 2
[0092] Embodiment 2: in composite latex (1) preparation process, do not add Al 2 (SO 4 ) 3 Agglomerating agent, all the other prescriptions and operation are with embodiment 1.
Embodiment 3
[0094] (1) Preparation of polyacrylate (ACR) composite latex
[0095] The seed of ACR composite latex and core layer composition are the same as embodiment 1, and shell layer composition is the mixed solution of 5.26g styrene (St), 9.74g MMA and 0.226g BDDA monomer. During the synthesis process, 0.12 g of SDS was added after the dropwise addition of the core layer monomer mixture. After continuing the insulation reaction for 2 hours, add 0.08g K 2 S 2 o 8 (No agglomeration agent was added before), start to add the shell layer monomer dropwise, and refer to Example 1 for the rest of the operations.
[0096] (2) Synthesis of ACR-g-VC emulsion resin
[0097] Adopt the composite latex prepared in the present embodiment (1) in this step synthesis, add the composite particle latex (according to the solid content calculation in the composite latex (1) of this example) of about 24g of solid content, operation procedure is the same as embodiment 1 (2). attached figure 2 It is a...
PUM
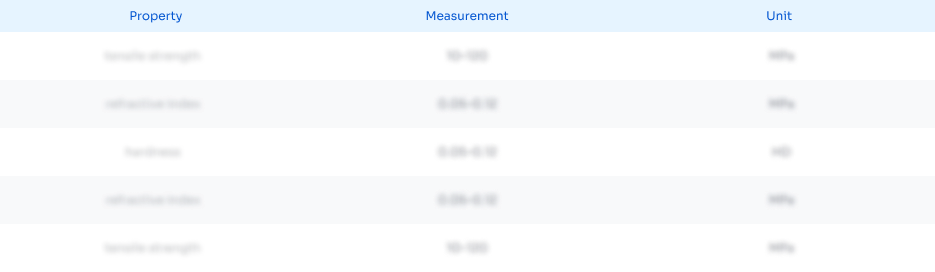
Abstract
Description
Claims
Application Information

- R&D
- Intellectual Property
- Life Sciences
- Materials
- Tech Scout
- Unparalleled Data Quality
- Higher Quality Content
- 60% Fewer Hallucinations
Browse by: Latest US Patents, China's latest patents, Technical Efficacy Thesaurus, Application Domain, Technology Topic, Popular Technical Reports.
© 2025 PatSnap. All rights reserved.Legal|Privacy policy|Modern Slavery Act Transparency Statement|Sitemap|About US| Contact US: help@patsnap.com