A coating method for composite toughened thin rods
A composite material and coating technology, which is applied in the coating field of composite toughened thin rods, can solve the problems of inappropriate modification of composite thin rods, difficult to find, etc., and achieves a simple method, improved interface performance, and good interface. performance effect
- Summary
- Abstract
- Description
- Claims
- Application Information
AI Technical Summary
Problems solved by technology
Method used
Image
Examples
Embodiment Construction
[0031] Further describe the present invention below in conjunction with embodiment and accompanying drawing thereof:
[0032] It is 0.55mm, the coating process of the coated thin rod of 400 order carbon fiber powder that adopt coating method of the present invention to prepare diameter to provide below:
[0033] Thin rod coating process such as figure 1 shown. A bundle of T300-3k carbon fiber enters the resin tank 2 to impregnate the resin, and then enters the initial forming mold 3, the initial forming mold 3, such as figure 2As shown, there is a circular through-hole mold cavity 301 with a length of 7 mm and a diameter of 0.50 mm.
[0034] Thin rod 10 enters in the coating chamber 4 that fills 400 mesh carbon fiber powders immediately after being pulled out from mold 3, and the total stroke (inner cavity length) of uncured thin rod in coating chamber 4 is 300mm, and the drawing of thin rod 10 The pulling speed is 1m / min. The length direction of the coating chamber 4 is ...
PUM
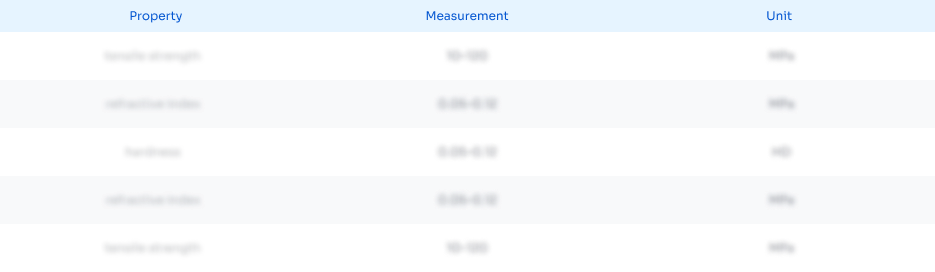
Abstract
Description
Claims
Application Information

- Generate Ideas
- Intellectual Property
- Life Sciences
- Materials
- Tech Scout
- Unparalleled Data Quality
- Higher Quality Content
- 60% Fewer Hallucinations
Browse by: Latest US Patents, China's latest patents, Technical Efficacy Thesaurus, Application Domain, Technology Topic, Popular Technical Reports.
© 2025 PatSnap. All rights reserved.Legal|Privacy policy|Modern Slavery Act Transparency Statement|Sitemap|About US| Contact US: help@patsnap.com