Method for preparing polyether ester polyalcohol
A technology of polyether ester polyol and small molecule polyether, which is applied in the field of preparation of polyether ester polyol, can solve the problems that the dynamic properties of polyurethane cannot reach the expected results, the strength and tensile properties of polyurethane are poor, and the operation is inconvenient. Achieve the effect of low cost, high conversion rate and strong practicability
- Summary
- Abstract
- Description
- Claims
- Application Information
AI Technical Summary
Problems solved by technology
Method used
Examples
Embodiment 1
[0019] Dissolve 10.0g potassium hexacyanocobaltate in 200ml deionized water to obtain 0.16mol / l potassium hexacyanocobaltate solution; dissolve 20.0g zinc chloride in 40ml deionized water to obtain 3.67mol / l zinc chloride solution; uniformly mix zinc chloride solution and potassium hexacyanocobaltate solution under vigorous stirring to obtain zinc hexacyanocobaltate precipitate. After the precipitation is separated, it is washed 3 times with deionized water, 200ml each time, and the washed precipitate is dried to constant weight under vacuum; the dried precipitate is placed in a closed container filled with ethylene glycol diethyl ether gas, and the precipitate Place to constant weight to obtain zinc hexacyanocobaltate ethylene glycol diethyl ether double metal complex catalyst.
[0020] In dry 1-liter autoclave, add 100g polycyclopropane ether glycol (hydroxyl value 160), 42g phthalic anhydride and 0.03g zinc hexacyanocobaltate ethylene glycol diethyl ether double metal compl...
Embodiment 2
[0022] In a dry 1 liter autoclave, add 100g polycyclopropane ether trihydric alcohol (hydroxyl value 160), 85g maleic anhydride and 0.04g zinc hexacyanocobaltate ethylene glycol diethyl ether double metal complex catalyst, nitrogen After the replacement, adjust the temperature of the kettle to 140°C, start electromagnetic stirring, inject 60g of epichlorohydrin after 2 hours, react for 10 hours, remove unreacted monomers and condensation products under reduced pressure, and record the weight of the obtained polymer after discharging . A polyether ester trihydric alcohol with a hydroxyl value of 66 was obtained with a yield of 100%.
Embodiment 3
[0024] In dry 1-liter autoclave, add 100g polycyclopropane ether tetrahydric alcohol (hydroxyl value 160), 60g succinic anhydride and 0.05g zinc hexacyanocobaltate ethylene glycol diethyl ether double metal complex catalyst, after nitrogen replacement, Adjust the temperature of the kettle to 160°C, start electromagnetic stirring, inject 20g of propylene oxide and 40g of ethylene oxide after 2 hours, react for 24 hours, remove unreacted monomers and condensation products under reduced pressure, and record the obtained polymer after discharging of weight. A polyether ester tetraol with a hydroxyl value of 80 was obtained with a yield of 95%.
PUM
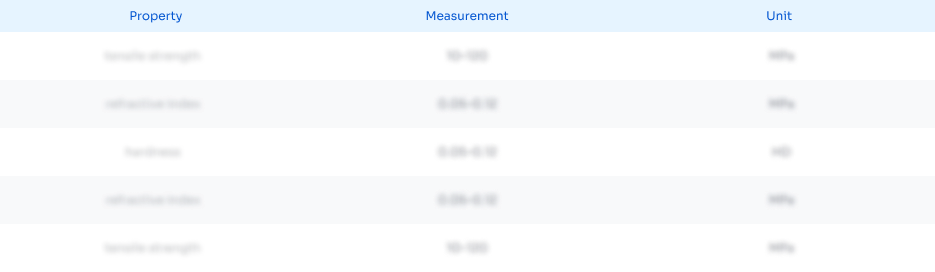
Abstract
Description
Claims
Application Information

- R&D
- Intellectual Property
- Life Sciences
- Materials
- Tech Scout
- Unparalleled Data Quality
- Higher Quality Content
- 60% Fewer Hallucinations
Browse by: Latest US Patents, China's latest patents, Technical Efficacy Thesaurus, Application Domain, Technology Topic, Popular Technical Reports.
© 2025 PatSnap. All rights reserved.Legal|Privacy policy|Modern Slavery Act Transparency Statement|Sitemap|About US| Contact US: help@patsnap.com