High-speed rail transit brake part casting structure and manufacturing process thereof
A technology of high-speed rails and brake parts, which is applied in the direction of manufacturing tools, casting molds, and casting mold components. It can solve problems such as defective products, eccentric cores, and inconvenient demoulding and picking up parts, so as to maintain stability and speed up flow effect
- Summary
- Abstract
- Description
- Claims
- Application Information
AI Technical Summary
Problems solved by technology
Method used
Image
Examples
Embodiment 1
[0046] See figure 1 As well as figure 2 As well as image 3 As well as Figure 4 As well as Figure 5 As well as Image 6 As well as Figure 7 As well as Figure 8 and Figure 9 It shows, a high -speed rail transit braking parts casting structure, including casting components for pouring for molding high -speed rail transit parts 1. Support component 2 and raising component 3; The assembly of the mold and the production of the cavity, and then use the support component 2 to support the support of the cast component 1, while generating vibration, which is convenient for the metal solution to enter, and facilitates the release of the formation in the later stage. Component 1 performs a combination and release.
[0047] Casting component 1 includes the upper box 11 and the lower box 12, of which the upper box 11 and the lower box 12 are filled with the first sand core 14 and the second sand core 15, and the first sand core 14 and the second sand core 15 are poured. There are 13 castings for...
Embodiment 2
[0061] The device provided by the present invention, the principle and the technical effects generated by the implementation of the same examples and the implementation example 1 are the same. To briefly describe, the example of the embodiments can be referred to the corresponding content in the Example 1.
[0062] Step 8: Put a certain amount of scrap steel into the mid -frequency electric furnace to melt into steel water, and when the temperature in the medium frequency electric furnace rises to 1040 ° C, then put it into steel ingots, raw iron, and return furnaces, and then scum. When the temperature in the Chinese frequency electric furnace rises to 1380 ° C, the iron is released. At this time, a certain amount of copper and molybdenum are poured with the iron water. In the 5th minute of pouring, the ultrasonic treatment is used for 3 minutes. After 15 minutes of pouring The weight percentage of the chemical components of the brakes casting, the percentage of the chemical comp...
PUM
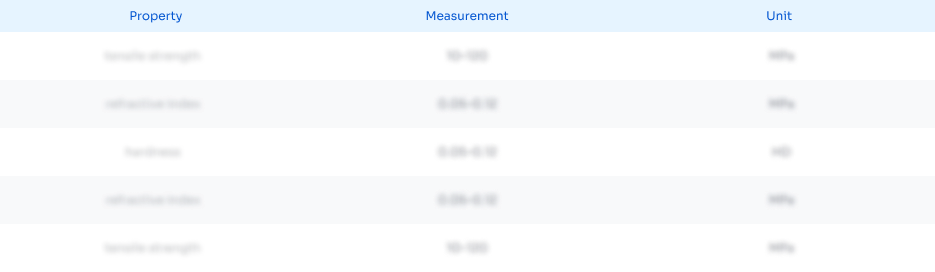
Abstract
Description
Claims
Application Information

- Generate Ideas
- Intellectual Property
- Life Sciences
- Materials
- Tech Scout
- Unparalleled Data Quality
- Higher Quality Content
- 60% Fewer Hallucinations
Browse by: Latest US Patents, China's latest patents, Technical Efficacy Thesaurus, Application Domain, Technology Topic, Popular Technical Reports.
© 2025 PatSnap. All rights reserved.Legal|Privacy policy|Modern Slavery Act Transparency Statement|Sitemap|About US| Contact US: help@patsnap.com