Low-speed heavy-duty bearing fault identification method and system, medium, equipment and terminal
A low-speed heavy-duty, fault identification technology, applied in neural learning methods, character and pattern recognition, machine/structural component testing, etc., can solve problems such as fluctuations in extraction results, affecting the accuracy of fault features, and frequency ambiguity. The effect of improving frequency concentration
- Summary
- Abstract
- Description
- Claims
- Application Information
AI Technical Summary
Problems solved by technology
Method used
Image
Examples
Embodiment Construction
[0098] In order to make the objectives, technical solutions and advantages of the present invention clearer, the present invention will be further described in detail below with reference to the embodiments. It should be understood that the specific embodiments described herein are only used to explain the present invention, but not to limit the present invention.
[0099] In view of the problems existing in the prior art, the present invention provides a method, system, medium, equipment and terminal for identifying faults of a low-speed heavy-load bearing. The present invention is described in detail below with reference to the accompanying drawings.
[0100] 1. Explain the embodiment. In order for those skilled in the art to fully understand how the present invention is specifically implemented, this part is an explanatory embodiment to expand the description of the technical solutions of the claims.
[0101] The invention proposes a low-speed heavy-load bearing fault iden...
PUM
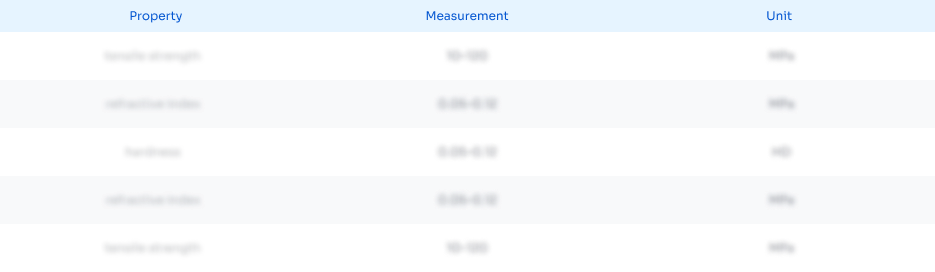
Abstract
Description
Claims
Application Information

- R&D Engineer
- R&D Manager
- IP Professional
- Industry Leading Data Capabilities
- Powerful AI technology
- Patent DNA Extraction
Browse by: Latest US Patents, China's latest patents, Technical Efficacy Thesaurus, Application Domain, Technology Topic, Popular Technical Reports.
© 2024 PatSnap. All rights reserved.Legal|Privacy policy|Modern Slavery Act Transparency Statement|Sitemap|About US| Contact US: help@patsnap.com