Comprehensive utilization process of red mud and coal gangue under action of short-process mechanical energy
A technology of coal gangue and mechanical energy, applied in the field of materials, can solve the problems of many steps, comprehensive utilization rate less than 20%, insufficient comprehensive utilization rate, etc., and achieve the effect of short process, strong adhesion between particles, and increased specific surface area
- Summary
- Abstract
- Description
- Claims
- Application Information
AI Technical Summary
Problems solved by technology
Method used
Image
Examples
Embodiment 1
[0037] Pour 30kg of red mud, 70kg of coal gangue and 10kg of water glass (30wt.%) additives into a planetary ball mill in turn, perform ball milling at a speed of 100rpm, react under the action of mechanical energy for 1h, and then unload the mixed material, at 70 ℃ The flowing hot air is dried for 12h, and the dry air flow is 1000m 3 / h, that is, to obtain the powder raw materials for the production of full-body bricks, denoted as A.
[0038] In this embodiment, the water in the raw material comes from water glass.
Embodiment 2
[0040] Pour 40kg of red mud, 60kg of coal gangue, and 10kg of water glass (30wt.%) additives into a planetary ball mill successively, carry out ball milling at a rotational speed of 100 rpm, and react under mechanical energy for 30 minutes, and then unload the mixed material. ℃ of flowing hot air for drying treatment for 12h, of which the dry air flow rate is 100m 3 / h, that is, to obtain the powder raw materials for the production of full-body bricks, denoted as B.
[0041] In this embodiment, the water in the raw material comes from water glass.
Embodiment 3
[0043]Pour 40kg of red mud, 60kg of coal gangue, 8kg of water glass (30wt.%), and 2kg of calcium sulfate additive into a planetary ball mill successively, and perform ball milling at a rotational speed of 100rpm, react under the action of mechanical energy for 30 minutes, and then unload the mixture. out, and dry at 70°C with flowing hot air for 12h, wherein the dry air flow is 2000m 3 / h, that is, to obtain the powder raw material for the production of full-body bricks, denoted as C.
[0044] In this embodiment, the water in the raw material comes from water glass.
PUM
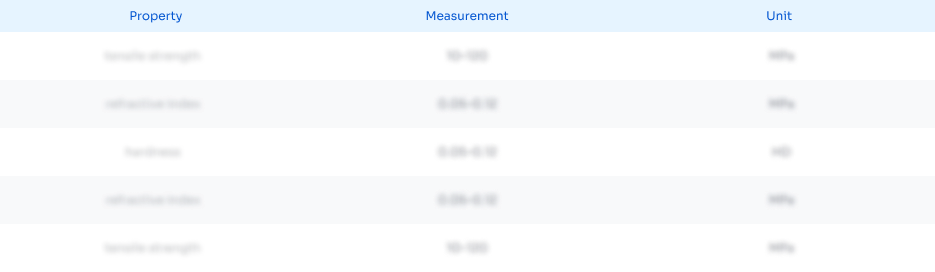
Abstract
Description
Claims
Application Information

- R&D
- Intellectual Property
- Life Sciences
- Materials
- Tech Scout
- Unparalleled Data Quality
- Higher Quality Content
- 60% Fewer Hallucinations
Browse by: Latest US Patents, China's latest patents, Technical Efficacy Thesaurus, Application Domain, Technology Topic, Popular Technical Reports.
© 2025 PatSnap. All rights reserved.Legal|Privacy policy|Modern Slavery Act Transparency Statement|Sitemap|About US| Contact US: help@patsnap.com