High-hardness and high-thermal-stability tantalum nitride block prepared based on domestic cubic press
A technology of high thermal stability, six-sided top press, applied in the field of preparing large-sized tantalum nitride blocks based on domestic six-sided top press, can solve the problems of low hardness of WC-type tantalum nitride, and achieve a simple preparation process , Broaden the prospect of industrial application, the effect of low temperature and pressure conditions
- Summary
- Abstract
- Description
- Claims
- Application Information
AI Technical Summary
Problems solved by technology
Method used
Image
Examples
Embodiment 1
[0018] Example 1: Take tantalum nitride powder (CoSn-type tantalum nitride with hexagonal structure or WC-type tantalum nitride with cubic structure) for grinding. Vacuum treatment, take out the vacuum-treated tantalum nitride powder, use a mold to pre-press the tantalum nitride into a cylindrical block, put the pressed cylindrical block into the graphite in the pyrophyllite synthesis block, and the upper and lower ends of the graphite tube are in turn Assemble the graphite sheet, molybdenum sheet and conductive steel ring. After assembling, put the synthetic block into the synthesis chamber of the large press, at a temperature of about 1000 ° C and a pressure of about 2 GPa, after about 20 minutes of heat preservation and pressure, the synthetic sintered block was taken out after cooling and depressurization, and the block WC- type tantalum nitride.
Embodiment 2
[0019] Example 2: Take tantalum nitride powder (CoSn-type tantalum nitride with hexagonal structure or WC-type tantalum nitride with cubic structure) for grinding. Vacuum sintering, take out the tantalum nitride powder after vacuum sintering, use a mold to pre-press the tantalum nitride into a cylindrical block, put the pressed cylindrical block into the graphite in the pyrophyllite synthesis block, and the upper and lower ends of the graphite tube are in turn Assemble the graphite sheet, molybdenum sheet and conductive steel ring. After assembly, put the synthesis block into the synthesis chamber of the large press. At a temperature of about 1400 ° C and a pressure of about 4 GPa, after about 45 minutes of heat preservation and pressure, the sintered block is taken out after cooling and depressurization. The block is WC- type tantalum nitride.
Embodiment 3
[0020] Example 3: Take tantalum nitride powder (CoSn-type tantalum nitride with hexagonal structure or WC-type tantalum nitride with cubic structure) for grinding. Vacuum sintering, take out the tantalum nitride powder after vacuum sintering, use a mold to pre-press the tantalum nitride into a cylindrical block, put the pressed cylindrical block into the graphite in the pyrophyllite synthesis block, and the upper and lower ends of the graphite tube are in turn Assemble the graphite sheet, molybdenum sheet and conductive steel ring. After assembly, put the synthesis block into the synthesis chamber of the large press. At a temperature of about 1600 ° C and a pressure of about 5 GPa, after about 30 minutes of heat preservation and pressure, the sintered block is taken out after cooling and depressurization. The block is WC- type tantalum nitride.
PUM
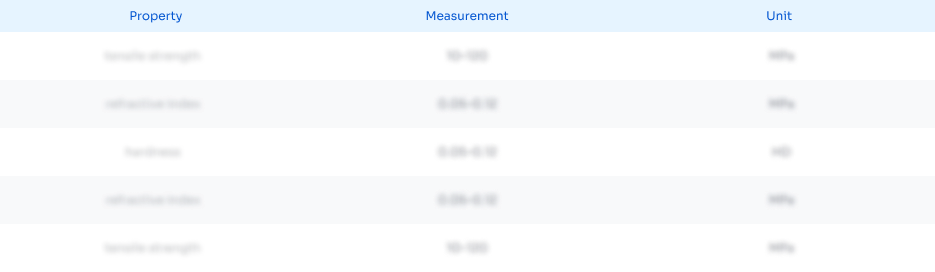
Abstract
Description
Claims
Application Information

- R&D
- Intellectual Property
- Life Sciences
- Materials
- Tech Scout
- Unparalleled Data Quality
- Higher Quality Content
- 60% Fewer Hallucinations
Browse by: Latest US Patents, China's latest patents, Technical Efficacy Thesaurus, Application Domain, Technology Topic, Popular Technical Reports.
© 2025 PatSnap. All rights reserved.Legal|Privacy policy|Modern Slavery Act Transparency Statement|Sitemap|About US| Contact US: help@patsnap.com