Method for improving castability of ultra-low carbon steel
A technology of ultra-low carbon steel and castability, which is applied in the field of molten steel refining, can solve problems such as difficulty in improving the castability of molten steel, and achieve the effects of effective treatment, promotion of collision growth, and improvement of castability
- Summary
- Abstract
- Description
- Claims
- Application Information
AI Technical Summary
Problems solved by technology
Method used
Image
Examples
Embodiment 1
[0066] like figure 1 and figure 2 As shown, a method for improving the castability of ultra-low carbon steel is provided, the method comprising:
[0067] S11. Obtain the incoming molten steel from RH refining to the station;
[0068] S12. Perform the second oxygen determination and temperature determination on the incoming molten steel to obtain the second oxygen content and temperature of the incoming molten steel;
[0069] S13. Obtain the target value of carbon content according to the second oxygen content and the temperature of the incoming molten steel;
[0070] S14. Carry out cyclic decarburization according to the target value of carbon content to obtain decarburized molten steel after RH refining cyclic decarburization;
[0071] S2. The first oxygen determination is performed on the decarburized molten steel to obtain the first oxygen content;
[0072] S3. according to the first oxygen content, obtain the required addition of aluminum-containing deoxidizer for deo...
Embodiment 2
[0086] Comparing Example 2 with Example 1, the difference between Example 2 and Example 1 is:
[0087] The first oxygen content was 350 ppm.
[0088] The conversion rate was taken as 94%.
[0089] In terms of mass fraction, the chemical composition of the high calcium aluminum slag ball includes: Ca: 25%, Al: 48%, and the rest are inevitable impurities.
[0090] The added amount of high calcium aluminum slag ball is 150kg.
[0091] The flow rate of bottom blowing is 40L / min, and the time of bottom blowing is 10min.
[0092] The second oxygen content was 550 ppm.
[0093] The temperature of the incoming molten steel was 1620°C.
Embodiment 3
[0095] Comparing Example 3 with Example 1, the difference between Example 3 and Example 1 is:
[0096] The first oxygen content was 450 ppm.
[0097] The conversion rate was taken as 92%.
[0098] In terms of mass fraction, the chemical composition of the high calcium aluminum slag ball includes: Ca: 25%, Al: 48%, and the rest are inevitable impurities.
[0099] The added amount of high calcium aluminum slag ball is 200kg.
[0100] The flow rate of bottom blowing is 100L / min, and the time of bottom blowing is 15min.
[0101] The second oxygen content was 750 ppm.
[0102] The temperature of the incoming molten steel was 1630°C.
PUM
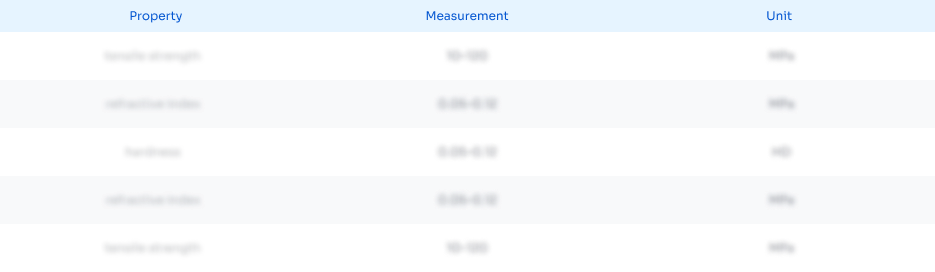
Abstract
Description
Claims
Application Information

- R&D
- Intellectual Property
- Life Sciences
- Materials
- Tech Scout
- Unparalleled Data Quality
- Higher Quality Content
- 60% Fewer Hallucinations
Browse by: Latest US Patents, China's latest patents, Technical Efficacy Thesaurus, Application Domain, Technology Topic, Popular Technical Reports.
© 2025 PatSnap. All rights reserved.Legal|Privacy policy|Modern Slavery Act Transparency Statement|Sitemap|About US| Contact US: help@patsnap.com