Composite flocculant for treating dye wastewater as well as preparation method and application of composite flocculant
A composite flocculant and dye wastewater technology, applied in chemical instruments and methods, textile industry wastewater treatment, water/sludge/sewage treatment, etc., can solve problems such as the impact of flocculation effect, achieve stable flocculant effect, improve form, stable effect
- Summary
- Abstract
- Description
- Claims
- Application Information
AI Technical Summary
Problems solved by technology
Method used
Examples
Embodiment 1
[0042] The composite flocculant for treating dye wastewater described in Example 1 is composed of the following raw materials in parts by weight: 0.6 part of cationic polyacrylamide, chlorinated poly-2-hydroxypropyl-1,1-N-dimethylformaldehyde 8 parts of base ammonium, 3 parts of cetyltrimethyl ammonium bromide, 3.5 parts of polydimethyldiallyl ammonium chloride, 1 part of polyethyleneimine, 7 parts of ferrous sulfate, 2 parts of sodium silicate , 8 parts of polyaluminum ferric sulfate, and 0.05 part of polyacrylic acid.
[0043] in:
[0044] The preparation method of cationic polyacrylamide consists of the following steps:
[0045] (1) Add N,N,N-trimethyl-3-(2-methacrylamido)-1-propylammonium chloride, acrylamide, disodium EDTA and deionized water to the In the reactor, stir to dissolve;
[0046] (2) Pass nitrogen into the reactor for 25min, then add the initiator, and continue to pass nitrogen for 15min;
[0047] (3) Stop the nitrogen flow and raise the temperature to the...
Embodiment 2
[0064] The composite flocculant for treating dye wastewater described in Example 2 is composed of the following raw materials in parts by weight: 0.5 part of cationic polyacrylamide, chlorinated poly-2-hydroxypropyl-1,1-N-dimethylformaldehyde 9 parts of base ammonium, 4 parts of cetyltrimethyl ammonium bromide, 3 parts of polydimethyldiallyl ammonium chloride, 0.8 parts of polyethyleneimine, 6 parts of ferrous sulfate, 2.5 parts of sodium silicate , 10 parts of polyaluminum ferric sulfate, and 0.08 parts of polyacrylic acid.
[0065] in:
[0066] The preparation method of cationic polyacrylamide consists of the following steps:
[0067] (1) Add N,N,N-trimethyl-3-(2-methacrylamido)-1-propylammonium chloride, acrylamide, disodium EDTA and deionized water to the In the reactor, stir to dissolve;
[0068] (2) Pass nitrogen into the reactor for 20min, then add the initiator, and continue to pass nitrogen for 15min;
[0069] (3) Stop the nitrogen flow and raise the temperature t...
Embodiment 3
[0086] The composite flocculant for treating dye wastewater described in Example 3 is composed of the following raw materials in parts by weight: 0.8 part of cationic polyacrylamide, chlorinated poly-2-hydroxypropyl-1,1-N-dimethylformaldehyde 7 parts of base ammonium, 5 parts of cetyltrimethyl ammonium bromide, 4.5 parts of polydimethyldiallyl ammonium chloride, 1.5 parts of polyethyleneimine, 5 parts of ferrous sulfate, 2 parts of sodium silicate , 9 parts of polyaluminum ferric sulfate, and 0.1 part of polyacrylic acid.
[0087] in:
[0088] The preparation method of cationic polyacrylamide consists of the following steps:
[0089] (1) Add N,N,N-trimethyl-3-(2-methacrylamido)-1-propylammonium chloride, acrylamide, disodium EDTA and deionized water to the In the reactor, stir to dissolve;
[0090] (2) Pass nitrogen into the reactor for 23min, then add the initiator, and continue to pass nitrogen for 14min;
[0091] (3) Stop the nitrogen flow and raise the temperature to t...
PUM
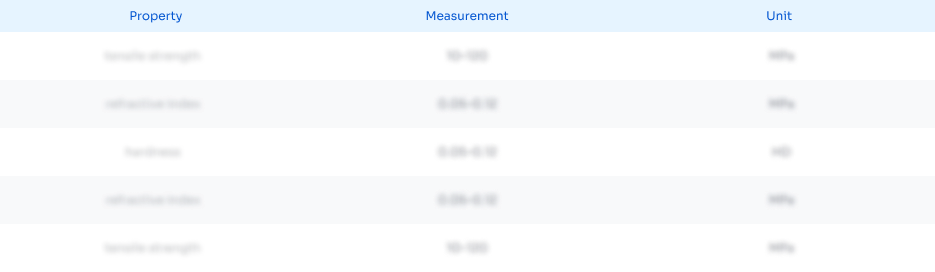
Abstract
Description
Claims
Application Information

- R&D Engineer
- R&D Manager
- IP Professional
- Industry Leading Data Capabilities
- Powerful AI technology
- Patent DNA Extraction
Browse by: Latest US Patents, China's latest patents, Technical Efficacy Thesaurus, Application Domain, Technology Topic, Popular Technical Reports.
© 2024 PatSnap. All rights reserved.Legal|Privacy policy|Modern Slavery Act Transparency Statement|Sitemap|About US| Contact US: help@patsnap.com