Wet-process powder forming preparation method containing cocoa tobacco auxiliary material and tobacco product
A technology of powder molding and auxiliary materials, which is applied in the fields of tobacco, tobacco processing, and tobacco preparation. It can solve the problems of woody or other miscellaneous gases, negative impact on sensory quality, and limited fragrance effect, etc., to achieve compactness and Excellent physical properties, improving the sensory quality of cigarettes, and reducing sensory stimulation
- Summary
- Abstract
- Description
- Claims
- Application Information
AI Technical Summary
Problems solved by technology
Method used
Image
Examples
preparation example Construction
[0081] For details, see figure 1 The flow chart shown in the dashed line and the solid line, specifically, the preparation method of the cocoa-containing cigarette adjuvant provided by this application includes the following steps:
[0082] (1) Preparation of ultrafine powder: use an oven to dry the cocoa to a moisture content of about 10% at 40°C, and use the ultrafine pulverization equipment to prepare the cocoa raw material pretreated in step (1) into 20-800 m cocoa ultrafine powder ;
[0083] (2) extraction: carry out solid-liquid separation after the cocoa ultrafine powder of step (1) and tobacco raw material are extracted respectively, obtain solid (cocoa ultrafine powder extract residue) and filtrate, such as figure 1 The dotted line is shown in the middle; or the tobacco raw material is extracted and then subjected to solid-liquid separation, and the cocoa ultrafine powder does not participate in the extraction, such as figure 1 shown in the solid line;
[0084] (3)...
Embodiment 1
[0089] Example 1: Preparation of Tobacco Sheet Sample 1 Containing Cocoa Smokable Excipients
[0090] Material selection: weigh 20 parts by weight of cocoa raw materials, 15 parts by weight of softwood pulp, and 65 parts by weight of tobacco raw materials as raw materials. Cocoa raw materials are husk and seed coat mixed in a mass ratio of 1:1.
[0091] Preparation of ultrafine powder: the cocoa raw material is prepared into D by ultrafine pulverization equipment 50 =50 mesh cocoa superfine powder;
[0092] Extraction: The raw materials (tobacco raw materials, plant fibers) and water were mixed at a weight ratio of 1:5, and the mixture was extracted at 50° C. for 1 h to obtain a solid part and a liquid part.
[0093] Pulping and papermaking: the solid part is pulped with a beating degree of 30°SR to obtain a slurry, and the cocoa ultrafine powder is added to the slurry at 5 parts by dry weight. At this time, the absolute dry weight of the slurry is 95 parts by weight, After...
Embodiment 2
[0096]Example 2: Preparation of Tobacco Sheet Sample 2 Containing Cocoa Smokable Excipients
[0097] Material selection: weigh 20 parts by weight of cocoa raw materials, 15 parts by weight of hardwood pulp, and 65 parts by weight of tobacco raw materials as raw materials. Cocoa raw material is husk.
[0098] Preparation of ultrafine powder: the cocoa raw material is prepared into D by ultrafine pulverization equipment 50 =500 mesh cocoa superfine powder;
[0099] Extraction: Mix the raw materials (tobacco raw materials, plant fibers) and water according to the weight ratio of 1:20, and extract the mixture at 90° C. for 5 hours to obtain a solid part and a liquid part.
[0100] Pulping and papermaking: the solid part is pulped with a beating degree of 65°SR to obtain a slurry, and the cocoa superfine powder is added to the slurry at 50 parts by weight, and the absolute dry weight of the slurry is 50 parts by weight at this time, After mixing evenly, use a dynamic paper forme...
PUM
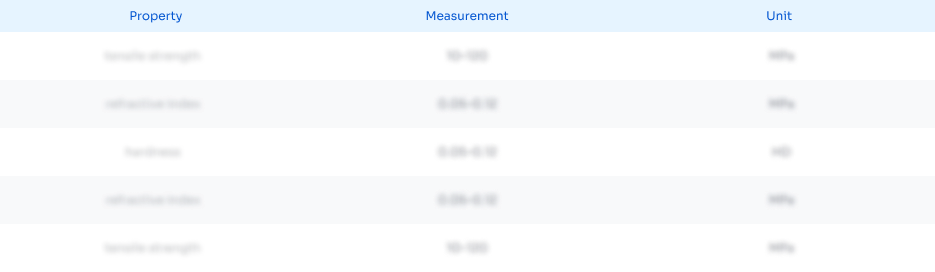
Abstract
Description
Claims
Application Information

- Generate Ideas
- Intellectual Property
- Life Sciences
- Materials
- Tech Scout
- Unparalleled Data Quality
- Higher Quality Content
- 60% Fewer Hallucinations
Browse by: Latest US Patents, China's latest patents, Technical Efficacy Thesaurus, Application Domain, Technology Topic, Popular Technical Reports.
© 2025 PatSnap. All rights reserved.Legal|Privacy policy|Modern Slavery Act Transparency Statement|Sitemap|About US| Contact US: help@patsnap.com