Machining process for metal flow guide nozzle of oil tank
A processing technology and diversion nozzle technology, which is applied in the field of auto parts production, can solve problems such as difficult management, cracking of workpieces, and inaccurate clamping and positioning consistency, so as to achieve beautiful and uniform appearance, improve internal quality, and save complicated procedures. Effect
- Summary
- Abstract
- Description
- Claims
- Application Information
AI Technical Summary
Problems solved by technology
Method used
Image
Examples
Embodiment Construction
[0080] Attached to the following Figure 1-31 To further illustrate the present invention,
[0081] The guide nozzle of the workpiece 5 to be processed by the present invention is as follows: image 3 As shown, the workpiece 5 is in the shape of a cone as a whole, and the top surface of the top cone is provided with a mouth hole 52, and a concave thread shape needs to be machined on the middle and lower cylinder to match the screwing of the fuel tank cover. The difficulty of processing workpieces with this structure is that after deep cylindrical drawing, annealing treatment is required, and then the thread structure on the barrel is processed, otherwise the workpiece will be cracked in a large proportion. In order to overcome this drawback of the prior art, the present invention proposes the following continuous processing and shaping process, and the "annealing" treatment is post-processed, so as to improve the consistency of the appearance of the finished product, and avoi...
PUM
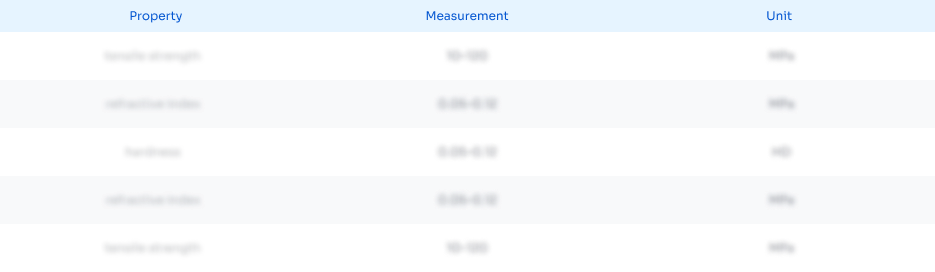
Abstract
Description
Claims
Application Information

- R&D
- Intellectual Property
- Life Sciences
- Materials
- Tech Scout
- Unparalleled Data Quality
- Higher Quality Content
- 60% Fewer Hallucinations
Browse by: Latest US Patents, China's latest patents, Technical Efficacy Thesaurus, Application Domain, Technology Topic, Popular Technical Reports.
© 2025 PatSnap. All rights reserved.Legal|Privacy policy|Modern Slavery Act Transparency Statement|Sitemap|About US| Contact US: help@patsnap.com