Pyrolysis harmless treatment method for sulfur-containing cyanidation leaching tailings
A technology of harmless treatment and cyanidation leaching, applied in chemical instruments and methods, improvement of process efficiency, removal of solid waste, etc. Unable to meet the detection standard of Class I solid waste, etc., to achieve the effect of efficient and harmless treatment and good degradation effect
- Summary
- Abstract
- Description
- Claims
- Application Information
AI Technical Summary
Problems solved by technology
Method used
Examples
Embodiment 1
[0016] 1) The cyanidation leaching sulfur-containing tailings are press-filtered into a filter cake with a moisture content of about 14%, and the sulfur content of the filter cake is determined to be 18.79%.
[0017] 2) Disperse the filter cake so that the maximum agglomeration particle size is less than 2cm, and set aside.
[0018] 3) Take 2kg of the disintegrated filter cake from the kiln head and add it into the rotary kiln, and pass the gas from the kiln head to the rotary kiln as air, and the flow rate is 0.6m 3 / h, the rotary kiln is heated, the air flow increases with the material at the same time, the pyrolysis treatment is carried out for 2 hours, the maximum pyrolysis temperature is controlled at 480 °C, the temperature of the material discharged at the end of the rotary kiln is controlled at 180 °C, and the CO concentration in the exhaust gas is controlled at 360 ~450mg / m 3 .
[0019] 4) After the pyrolysis treatment of the tailings, it was determined that the tot...
Embodiment 2
[0021] 1) Press filter the cyanidation leaching sulfur-containing tailings into a filter cake with a moisture content of about 14%, and the sulfur content of the filter cake is determined to be 24.12%.
[0022] 2) Disperse the filter cake so that the maximum agglomeration particle size is less than 2cm, and set aside.
[0023] 3) Take 2kg of the disintegrated filter cake from the kiln head and add it into the rotary kiln, and pass the gas from the kiln head to the rotary kiln as air with a flow rate of 0.7m 3 / h, the rotary kiln is heated, the air flow increases with the material at the same time, and the pyrolysis treatment is carried out for 2 hours. ~420mg / m 3 .
[0024] 4) After the pyrolysis treatment of the tailings, it was determined: the total cyanide content of the sample toxic leaching was 0.18mg / L, the pH value was 7.89, the SO 2 The highest concentration is 6mg / m 3 .
PUM
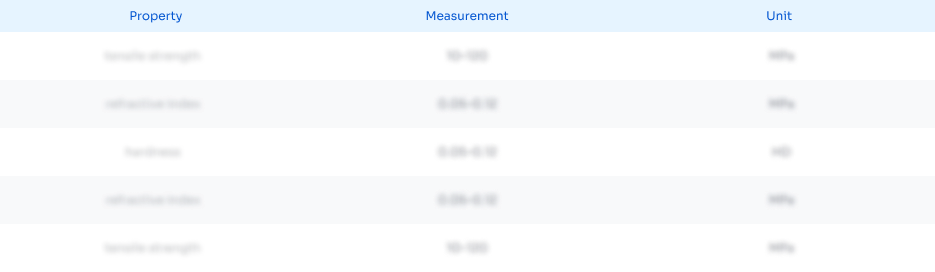
Abstract
Description
Claims
Application Information

- R&D
- Intellectual Property
- Life Sciences
- Materials
- Tech Scout
- Unparalleled Data Quality
- Higher Quality Content
- 60% Fewer Hallucinations
Browse by: Latest US Patents, China's latest patents, Technical Efficacy Thesaurus, Application Domain, Technology Topic, Popular Technical Reports.
© 2025 PatSnap. All rights reserved.Legal|Privacy policy|Modern Slavery Act Transparency Statement|Sitemap|About US| Contact US: help@patsnap.com