Shielding cover shape design method capable of modulating cooling airflow form in narrow space
A technology of cooling air flow and design method, applied in computer-aided design, CAD circuit design, calculation, etc., can solve the problems of restricting cooling air heat dissipation potential, decreasing device reliability, low surface convection heat transfer coefficient, etc., to achieve precise control of shielding Effects of hood size, reduced number of design variables, simplified post-processing
- Summary
- Abstract
- Description
- Claims
- Application Information
AI Technical Summary
Problems solved by technology
Method used
Image
Examples
Embodiment Construction
[0124] The present invention will be described in detail below with reference to the embodiments and accompanying drawings.
[0125] like figure 1 As shown in the figure, a shape design method of a shield cover that can modulate the cooling airflow pattern in a narrow space includes the following steps:
[0126] 1) Configure the initial parameterized level set component layout, and evenly distribute n closed B-spline curve shield shape parameterized level set components in the design domain on the PCB chip, each parameterized level set component contains the component center coordinates (x c ,y c ), the distance d from the 12 control points to the center i ,i=1,...,10, then the design variables of each closed B-spline parameterized level set component can be expressed as: ξ i =[x i ,y i ,d 1 ,…,d 10 ] T ; in each shield there is a power electronic component described by a hyperelliptic curve parameterized level set component, including the component center coordinates ...
PUM
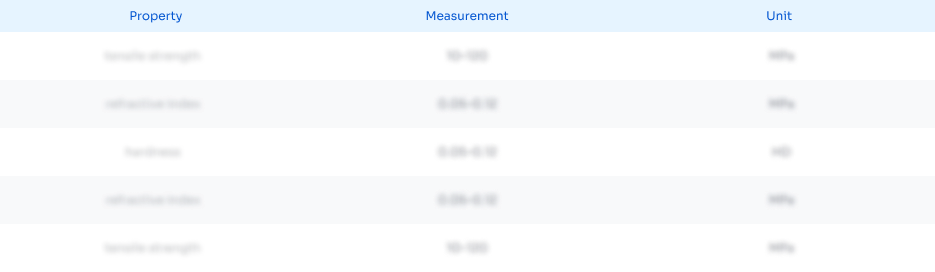
Abstract
Description
Claims
Application Information

- R&D
- Intellectual Property
- Life Sciences
- Materials
- Tech Scout
- Unparalleled Data Quality
- Higher Quality Content
- 60% Fewer Hallucinations
Browse by: Latest US Patents, China's latest patents, Technical Efficacy Thesaurus, Application Domain, Technology Topic, Popular Technical Reports.
© 2025 PatSnap. All rights reserved.Legal|Privacy policy|Modern Slavery Act Transparency Statement|Sitemap|About US| Contact US: help@patsnap.com