Micro multi-channel boiling heat exchange type uniform-temperature cooling plate
A boiling heat exchange and multi-channel technology, applied in indirect heat exchangers, lighting and heating equipment, climate sustainability, etc., can solve the problems of heat exchanger temperature drop, heat transfer coefficient drop, excessive thermal stress, etc. Achieve the effect of improving temperature uniformity and ensuring high uniformity
- Summary
- Abstract
- Description
- Claims
- Application Information
AI Technical Summary
Problems solved by technology
Method used
Image
Examples
Embodiment 1
[0032] A tiny multi-channel boiling heat-exchange type uniform temperature cooling plate, comprising a cooling liquid inlet channel 1 on the left, four cooling liquid boiling combination multi-channels 2 evenly distributed along the vertical direction at the middle position, and a boiling gas outlet on the right Channel 3; the liquid cooling medium is input from the cooling liquid inlet channel 1 to the four cooling liquid boiling combination multi-channels 2, exchanges heat with the cooled object on the side wall of the cooling plate, boils and vaporizes, and finally exits from the boiling gas outlet Channel 3 discharges.
[0033] like figure 1 As shown, the cooling liquid inlet channel 1 and the boiling gas outlet channel 3 are symmetrically arranged with respect to the cooling liquid boiling combined multi-channel 2;
[0034] The cooling liquid inlet channel 1 adopts a trapezoidal manifold structure that tapers along the flow direction of the liquid cooling working medium...
Embodiment 2
[0046] like image 3 As shown in the figure, this embodiment is basically the same as the embodiment 1, the only difference is that: the cooling liquid inlet channel 1 and the boiling gas outlet channel 3 both adopt a branched manifold structure, and the distribution direction of each pipe of the branched manifold structure is the same as that of the cooling liquid. The lateral directions of the boiling combined multi-channels 2 are parallel, and the total liquid inlet 11 of the cooling liquid inlet channel 1 and the gas total outlet 31 of the boiling gas outlet channel 3 are both located at the header end of the branched manifold structure.
Embodiment 1
[0047] Compared with Embodiment 1, this embodiment is more suitable for the even distribution of the liquid cooling medium under the conveying of the driving head, and the uniform distribution effect is better.
[0048] A verification calculation is performed for the above two embodiments, wherein the calculation adopts HFE-7000 working fluid, and its saturated boiling point under normal pressure is 307.15K. The obtained cloud image is in the shape of horizontal lines, which is completely different from the surface temperature cloud image of the traditional parallel flow micro multi-channel cooling plate. For details, see Figure 4 and Figure 5 ;
[0049] Figure 4 and Figure 5 The surface temperature nephogram of the conventional parallel flow micro-multi-channel cooling plate and the surface temperature nephogram of the uniform temperature cooling plate of the present invention (unit: K) are respectively represented. It can be clearly seen from the figures that the The...
PUM
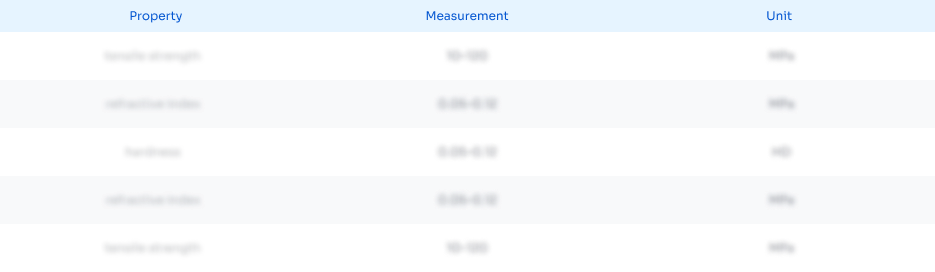
Abstract
Description
Claims
Application Information

- R&D Engineer
- R&D Manager
- IP Professional
- Industry Leading Data Capabilities
- Powerful AI technology
- Patent DNA Extraction
Browse by: Latest US Patents, China's latest patents, Technical Efficacy Thesaurus, Application Domain, Technology Topic, Popular Technical Reports.
© 2024 PatSnap. All rights reserved.Legal|Privacy policy|Modern Slavery Act Transparency Statement|Sitemap|About US| Contact US: help@patsnap.com