High-temperature alloy double-roller cast rolling process
A superalloy, casting and rolling technology, applied in the field of superalloy twin-roll casting and rolling technology, can solve problems such as unevenness, bulging, leakage and solidification structure, and achieve the effects of improving production efficiency, ensuring stability and reducing production costs.
- Summary
- Abstract
- Description
- Claims
- Application Information
AI Technical Summary
Problems solved by technology
Method used
Image
Examples
Embodiment 1
[0024] For the Inconel 718 alloy, the twin-roll casting and rolling process is used to produce it. The specific steps are as follows: 1) take 30kg of Inconel 718 alloy raw material for standby, put it into a crucible in a vacuum melting furnace for melting, and heat it up to 1500 ° C for 5 minutes; The tundish, casting and rolling unit, cooling and shearing components are all placed in the vacuum protection cover; while the alloy raw material is melted in step 1), the vacuum protection cover is evacuated to keep the vacuum degree at 10 -1 Below pa, then pour the completely melted alloy liquid into the baked tundish placed in the vacuum protective cover, let stand for 5 minutes, and use the tundish heating device to heat and keep the alloy liquid while standing; 3) When the temperature of the alloy liquid reaches 1500°C and the standing time meets the requirements, the alloy liquid is cast into the water-cooled rolls of the casting and rolling unit to realize the casting and rol...
Embodiment 2
[0030] Inconel 625 alloy production was carried out by adopting the twin-roll casting and rolling process. The specific operations were: 1) put the crucible in the vacuum melting furnace, take 25kg of Inconel 625 alloy raw material and put it into the crucible for melting, and heat up to 1550° C. for 5 minutes; 2) Put the tundish, casting and rolling unit, cooling and shearing components in the vacuum protection cover; while the alloy raw material is melted in step 1), vacuumize the vacuum protection cover to keep the vacuum degree at 10 -1 Below pa, then pour the completely melted alloy liquid into the baked tundish placed in the vacuum protective cover, let stand for 4 minutes, and use the tundish heating device to heat the alloy liquid while standing; 3) When the temperature of the alloy liquid reaches 1520 °C and the standing time meets the requirements, the alloy liquid is cast into the water-cooled rolls of the casting-rolling unit to realize the casting-rolling forming o...
PUM
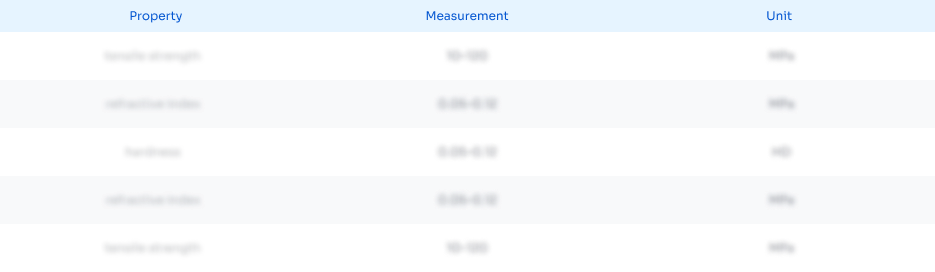
Abstract
Description
Claims
Application Information

- R&D
- Intellectual Property
- Life Sciences
- Materials
- Tech Scout
- Unparalleled Data Quality
- Higher Quality Content
- 60% Fewer Hallucinations
Browse by: Latest US Patents, China's latest patents, Technical Efficacy Thesaurus, Application Domain, Technology Topic, Popular Technical Reports.
© 2025 PatSnap. All rights reserved.Legal|Privacy policy|Modern Slavery Act Transparency Statement|Sitemap|About US| Contact US: help@patsnap.com