Manufacturing method of ultra-thin copper thick printed circuit board
A technology for printed circuit board and production method, which is applied in the directions of laminated printed circuit board, printed circuit, printed circuit manufacturing, etc., can solve the problems of inconsistent with the production concept, high production cost, large resource consumption, etc.
- Summary
- Abstract
- Description
- Claims
- Application Information
AI Technical Summary
Problems solved by technology
Method used
Examples
Embodiment 1
[0039] A method for making an ultra-thin copper-thick printed circuit board, which is characterized by comprising the following steps: cutting material—inner layer circuit—pressing—drilling—electrochemical copper plating—outer layer dry film—acidic Etching - AOI - post process.
[0040] Further, in the lamination process, a release film is used to complete the lamination process to form a copper-free multilayer printed circuit board on the outer layer.
[0041] Further, after the lamination process is completed, an optical core board is formed.
[0042] Further, after the drilling process is completed, a chemical degumming process is used to remove the hole wall and residual drilling dirt.
[0043] Further, after the chemical degumming process is completed, ultrasonic waves are used to treat the grooves and spikes generated by the degumming process.
[0044] Further, the electrolytic copper plating process includes the following steps:
[0045] S1. Adopt catalytic reduction...
Embodiment 2
[0055] A method for making an ultra-thin copper-thick printed circuit board, which is characterized by comprising the following steps: cutting material—inner layer circuit—pressing—drilling—electrochemical copper plating—outer layer dry film—acidic Etching - AOI - post process.
[0056] Further, in the lamination process, a release film is used to complete the lamination process to form a copper-free multilayer printed circuit board on the outer layer.
[0057] Further, after the lamination process is completed, an optical core board is formed.
[0058] Further, after the drilling process is completed, a chemical degumming process is used to remove the hole wall and residual drilling dirt.
[0059] Further, after the chemical degumming process is completed, ultrasonic waves are used to treat the grooves and spikes generated by the degumming process.
[0060] Further, the electrolytic copper plating process includes the following steps:
[0061] S1. Adopt catalytic reduction s...
Embodiment 3
[0071] A method for making an ultra-thin copper-thick printed circuit board, which is characterized by comprising the following steps: cutting material—inner layer circuit—pressing—drilling—electrochemical copper plating—outer layer dry film—acidic Etching - AOI - post process.
[0072] Further, in the lamination process, a release film is used to complete the lamination process to form a copper-free multilayer printed circuit board on the outer layer.
[0073] Further, after the lamination process is completed, an optical core board is formed.
[0074] Further, after the drilling process is completed, a chemical degumming process is used to remove the hole wall and residual drilling dirt.
[0075] Further, after the chemical degumming process is completed, ultrasonic waves are used to treat the grooves and spikes generated by the degumming process.
[0076] Further, the electrolytic copper plating process includes the following steps:
[0077] S1. Adopt catalytic reduction...
PUM
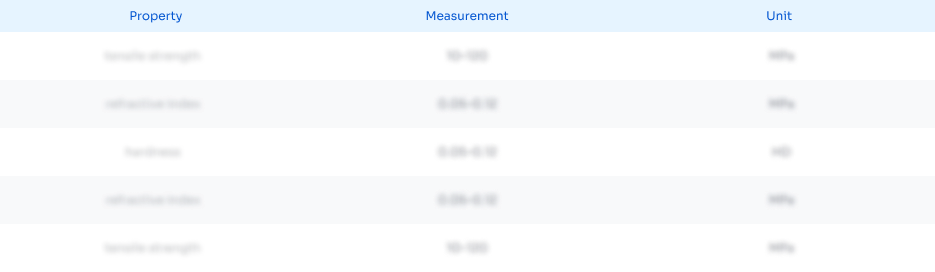
Abstract
Description
Claims
Application Information

- R&D
- Intellectual Property
- Life Sciences
- Materials
- Tech Scout
- Unparalleled Data Quality
- Higher Quality Content
- 60% Fewer Hallucinations
Browse by: Latest US Patents, China's latest patents, Technical Efficacy Thesaurus, Application Domain, Technology Topic, Popular Technical Reports.
© 2025 PatSnap. All rights reserved.Legal|Privacy policy|Modern Slavery Act Transparency Statement|Sitemap|About US| Contact US: help@patsnap.com