Production process and equipment of Freon-resistant composite enameled wire with glass fiber wrapping
A Freon-resistant and glass-filament-resistant technology, which is applied in the directions of transportation and packaging, delivery of filamentous materials, and insulation of conductors/cables, etc., can solve problems such as inability to dip enamelled wires, reduce production efficiency of enameled wires, and impossibility of dipping enameled wires, etc., to achieve The effect of improving the efficiency of dipping paint, low operating cost, and convenient reprocessing
- Summary
- Abstract
- Description
- Claims
- Application Information
AI Technical Summary
Problems solved by technology
Method used
Image
Examples
Embodiment 1
[0062] Freon-resistant composite enameled wire wrapped with glass filaments, see figure 1 , whose production involves the following steps:
[0063] S1. Use a copper wire body with clean and smooth appearance, no burrs, scratches, oxide layers and oil stains, and then enter the softening furnace for preheating;
[0064] S2. Then use the guide clamp to quickly and accurately guide the wire body, and then use the varnish dipping device to impregnate the copper wire body with Freon-resistant insulating varnish;
[0065] S3. Then the processing device can cure the wire body after dipping paint. The temperature of the first evaporation zone inside the curing furnace is controlled at 240°C, the temperature of the second evaporation zone is controlled at 280°C, the furnace temperature of the first curing zone is controlled at 400°C, and the temperature of the second curing zone is controlled at 400°C. Zone furnace temperature is controlled at 430°C;
[0066] S4. Use single-layer gla...
Embodiment 2
[0070] Freon-resistant composite enameled wire wrapped with glass filaments, see figure 1 , whose production involves the following steps:
[0071] S1. Use a copper wire body with clean and smooth appearance, no burrs, scratches, oxide layers and oil stains, and then enter the softening furnace for preheating;
[0072] S2. Then use the guide clamp to quickly and accurately guide the wire body, and then use the varnish dipping device to impregnate the copper wire body with Freon-resistant insulating varnish;
[0073] S3. Then the processing device can cure the wire body after dipping paint. The temperature of the first evaporation zone inside the curing furnace is controlled at 250°C, the temperature of the second evaporation zone is controlled at 290°C, the furnace temperature of the first curing zone is controlled at 410°C, and the temperature of the second curing zone is controlled at 410°C. Zone furnace temperature is controlled at 440°C;
[0074] S4. Use single-layer gla...
Embodiment 3
[0078] Freon-resistant composite enameled wire wrapped with glass filaments, see figure 1 , whose production involves the following steps:
[0079] S1. Use a copper wire body with clean and smooth appearance, no burrs, scratches, oxide layers and oil stains, and then enter the softening furnace for preheating;
[0080] S2. Then use the guide clamp to quickly and accurately guide the wire body, and then use the varnish dipping device to impregnate the copper wire body with Freon-resistant insulating varnish;
[0081] S3. Then the processing device can cure the wire body after dipping paint. The temperature of the first evaporation zone inside the curing furnace is controlled at 260°C, the temperature of the second evaporation zone is controlled at 320°C, the furnace temperature of the first curing zone is controlled at 420°C, and the temperature of the second curing zone is controlled at 420°C. Zone furnace temperature is controlled at 450°C;
[0082] S4. Use single-layer gla...
PUM
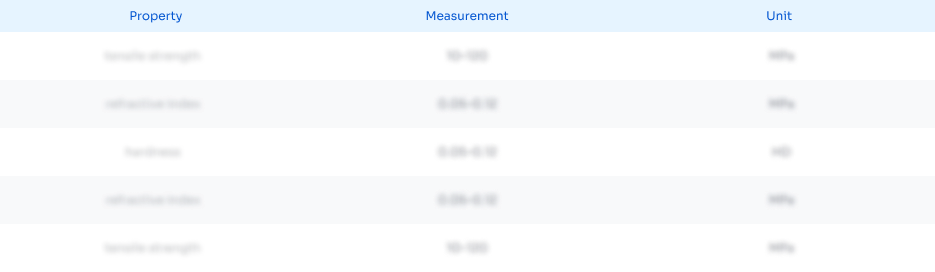
Abstract
Description
Claims
Application Information

- R&D
- Intellectual Property
- Life Sciences
- Materials
- Tech Scout
- Unparalleled Data Quality
- Higher Quality Content
- 60% Fewer Hallucinations
Browse by: Latest US Patents, China's latest patents, Technical Efficacy Thesaurus, Application Domain, Technology Topic, Popular Technical Reports.
© 2025 PatSnap. All rights reserved.Legal|Privacy policy|Modern Slavery Act Transparency Statement|Sitemap|About US| Contact US: help@patsnap.com