Iron ore mixed ore beneficiation process
A technology for mixing ore and iron ore, applied in solid separation, chemical instruments and methods, cyclone devices, etc., can solve the problem of large cyclic load of vertical mill equipment, magnetite occupying hematite separation space, and product particle size distribution. Unreasonable and other problems, to achieve the effect of improving grinding efficiency
- Summary
- Abstract
- Description
- Claims
- Application Information
AI Technical Summary
Problems solved by technology
Method used
Image
Examples
Embodiment 1
[0032] Such as figure 1 As shown, the raw ore grade of Dahongshan mineral processing scale is 4.8 million td with an annual processing capacity of 33.50%, the magnetic iron occupancy rate is 18%, and the magnetite and hematite mixed ore with a silicon content of 32.5% undergoes a ф1200 / 160 cycle The crusher is crushed to the ore sample with a particle size of -250mm. The ore sample is ground into a mineral powder with a particle size of -6mm by a Φ8.53×4.27m semi-autogenous mill. -6mm) into the pump pool; the materials in the pump pool are pumped into two identical Φ660 cyclones respectively; the qualified particle size (overflow pulp) after grading by the Φ660 cyclone is respectively subjected to a section of weak magnetic A and a section of weak Magnetic B; the underflow (coarse-grained pulp) of cyclones A and B returns to the pump pool after passing through the ball mill;
[0033] A section of weak magnetic tailings A and a section of weak magnetic tailings B are screened ...
PUM
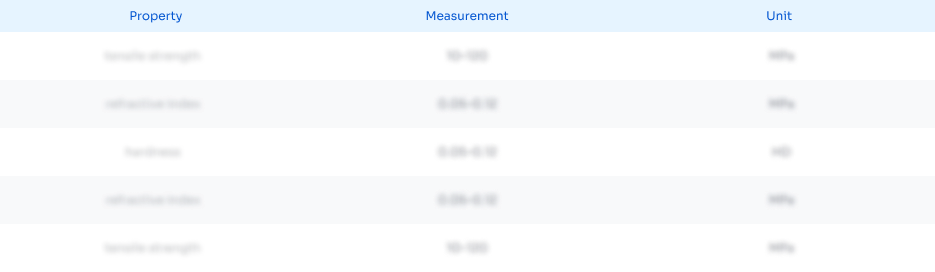
Abstract
Description
Claims
Application Information

- R&D Engineer
- R&D Manager
- IP Professional
- Industry Leading Data Capabilities
- Powerful AI technology
- Patent DNA Extraction
Browse by: Latest US Patents, China's latest patents, Technical Efficacy Thesaurus, Application Domain, Technology Topic, Popular Technical Reports.
© 2024 PatSnap. All rights reserved.Legal|Privacy policy|Modern Slavery Act Transparency Statement|Sitemap|About US| Contact US: help@patsnap.com