Low-carbon ultralow-sulfur pure iron smelting method
A technology of ultra-low sulfur pure iron and smelting methods, applied in the manufacture of converters, etc., can solve the problems of human health hazards, unfavorable on-site production, etc., and achieve the effect of avoiding sulfur return
- Summary
- Abstract
- Description
- Claims
- Application Information
AI Technical Summary
Problems solved by technology
Method used
Examples
Embodiment 1
[0025] Smelting low-carbon ultra-low sulfur pure iron DYCT-3, the composition requirements are C≤0.025%, Mn≤0.03%, P≤0.005%, S≤0.001%, and the nominal capacity of the converter is 260 tons.
[0026] DYCT-3 method for smelting low-carbon ultra-low-sulfur pure iron, molten iron pretreatment-converter double slag smelting-RH decarburization-LF dephosphorization-liquid steel slag removal-LF desulfurization-continuous casting; specifically includes:
[0027] 1. Hot metal pretreatment: the gross weight of iron folded between pouring tanks is 397 tons; iron selection before production, hot metal S = 0.024%, P = 0.113%, Ti = 0.0325%; hot metal pretreatment desulfurization content of 0.001%;
[0028] 2. Before the converter is produced, use molten iron with slag removal S≤0.005% in the furnace to rinse the furnace twice;
[0029] 3. Converter double slag smelting:
[0030] Add 30 tons of pure iron special scrap steel to the converter, start oxygen blowing, add slagging material for 50...
Embodiment 2
[0056] Smelting low-carbon ultra-low sulfur pure iron DYCT-3, the composition requirements are C≤0.025%, Mn≤0.03%, P≤0.005%, S≤0.001%, and the nominal capacity of the converter is 200 tons.
[0057] DYCT-3 method for smelting low-carbon ultra-low-sulfur pure iron, molten iron pretreatment-converter double slag smelting-RH decarburization-LF dephosphorization-liquid steel slag removal-LF desulfurization-continuous casting; specifically includes:
[0058] 1. Hot metal pretreatment: the gross weight of iron folded between pouring tanks is 308 tons; iron selection before production, hot metal S = 0.028%, P = 0.097%, Ti = 0.0228%; hot metal pretreatment desulfurization content of 0.001%;
[0059] 2. Before the converter is produced, use molten iron with slag removal S≤0.005% in the furnace to rinse the furnace twice;
[0060] 3. Converter double slag smelting:
[0061] Add 20.3 tons of scrap steel for pure iron to the converter, start oxygen blowing, add slagging material for 50 s...
PUM
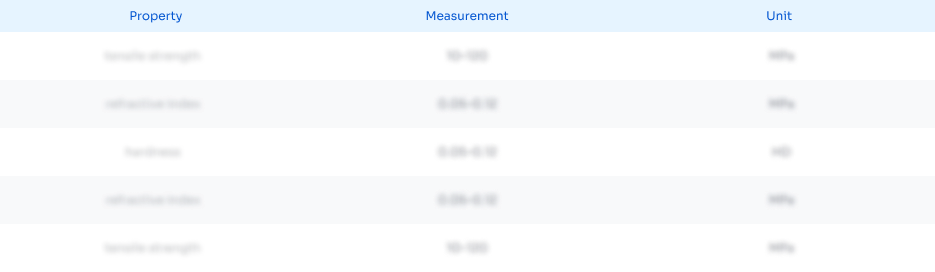
Abstract
Description
Claims
Application Information

- R&D
- Intellectual Property
- Life Sciences
- Materials
- Tech Scout
- Unparalleled Data Quality
- Higher Quality Content
- 60% Fewer Hallucinations
Browse by: Latest US Patents, China's latest patents, Technical Efficacy Thesaurus, Application Domain, Technology Topic, Popular Technical Reports.
© 2025 PatSnap. All rights reserved.Legal|Privacy policy|Modern Slavery Act Transparency Statement|Sitemap|About US| Contact US: help@patsnap.com