Four-step forging forming process for automobile hub axle tube
A technology for forging and forming of automobile wheels, which is applied in the direction of manufacturing tools, metal processing equipment, forging/pressing/hammer devices, etc., and can solve problems such as the strength and wear resistance of the hub shaft tube affecting the use effect
- Summary
- Abstract
- Description
- Claims
- Application Information
AI Technical Summary
Problems solved by technology
Method used
Image
Examples
Embodiment Construction
[0020] The following will clearly and completely describe the technical solutions in the embodiments of the present invention with reference to the accompanying drawings in the embodiments of the present invention. Obviously, the described embodiments are only some, not all, embodiments of the present invention. Based on the embodiments of the present invention, all other embodiments obtained by persons of ordinary skill in the art without making creative efforts belong to the protection scope of the present invention.
[0021] see figure 1 , the present invention provides a technical solution: a four-step forging molding process for an automobile hub shaft tube, comprising the following steps:
[0022] S1. Raw material pretreatment: select a bar with a suitable length, place it inside the heating furnace for heating, and control the heating temperature between 350°C and 450°C;
[0023] S2. Preliminary forging: take the heated bar out of the heating furnace, place it in the p...
PUM
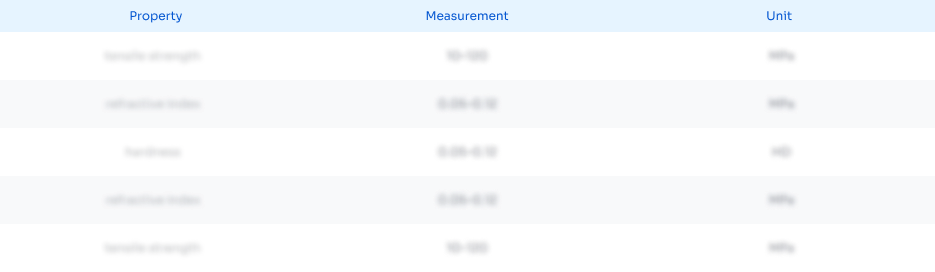
Abstract
Description
Claims
Application Information

- R&D Engineer
- R&D Manager
- IP Professional
- Industry Leading Data Capabilities
- Powerful AI technology
- Patent DNA Extraction
Browse by: Latest US Patents, China's latest patents, Technical Efficacy Thesaurus, Application Domain, Technology Topic, Popular Technical Reports.
© 2024 PatSnap. All rights reserved.Legal|Privacy policy|Modern Slavery Act Transparency Statement|Sitemap|About US| Contact US: help@patsnap.com