A process for forging plates from heavy steel ingots
A technology for steel ingots and plates, which is applied in the field of forging plates for heavy steel ingots, can solve problems such as changes in the crystallization status of the internal structure, improper deformation, and slow recrystallization speed, so as to eliminate intragranular micro-cracks, ensure forging quality, The effect of eliminating intragranular segregation
- Summary
- Abstract
- Description
- Claims
- Application Information
AI Technical Summary
Problems solved by technology
Method used
Examples
Embodiment 1
[0022] A process for forging plates from heavy steel ingots, comprising the following steps:
[0023] S1: Insulation heating, heating ton-level steel ingots in a heating furnace, the temperature of the heating furnace is 1200°C, and heat preservation and heating for 14h~16h;
[0024] S2: rough forging, the steel ingot after high temperature diffusion in S1 is rough forged, and the deformation of the steel ingot is 45%, the rough forging forging ratio is 2, after the completion, return to the furnace for heating, and the furnace temperature is 1190°C;
[0025] S3: Forging and drawing the slab, forging and drawing the slab after returning the steel ingot to the furnace for heating in S2, the deformation of the steel ingot is 25%, and then returning the steel ingot to the furnace for heating, and the furnace temperature is 1150°C;
[0026] S4: Secondary forging and drawing, the steel ingot in S3 is returned to the furnace and heated to forge and draw the slab again, the deformati...
Embodiment 2
[0030] A process for forging plates from heavy steel ingots, comprising the following steps:
[0031] S1: Insulation heating, heating ton-level steel ingots in a heating furnace, the temperature of the heating furnace is 1250 ° C, and heat preservation and heating for 16 hours;
[0032] S2: rough forging, the steel ingot after high temperature diffusion in S1 is rough forged, and the deformation of the steel ingot is 45%, the rough forging forging ratio is 2, after the completion, return to the furnace for heating, and the furnace temperature is 1210°C;
[0033] S3: Forging and drawing the slab, forging and drawing the slab after returning the steel ingot to the furnace for heating in S2, the deformation of the steel ingot is 25%, and then returning the steel ingot to the furnace for heating, and the furnace temperature is 1170°C;
[0034] S4: Secondary forging and drawing, the steel ingot in S3 is returned to the furnace and heated to forge and draw the slab again, the deform...
Embodiment 3
[0038] A process for forging plates from heavy steel ingots, comprising the following steps:
[0039] S1: heat preservation and heating, heat the steel ingot of ton level in the heating furnace, the temperature of the heating furnace is 1220 ℃, and heat preservation and heating for 15 hours;
[0040] S2: rough forging, the steel ingot after high temperature diffusion in S1 is rough forged, and the deformation of the steel ingot is 50%, the rough forging forging ratio is 2, after the completion, return to the furnace for heating, and the furnace temperature is 1200°C;
[0041] S3: forging and drawing the slab, forging and drawing the steel ingot after being heated in the furnace in S2, the deformation of the steel ingot is 30%, and then returning the steel ingot to the furnace for heating, and the furnace temperature is 1160°C;
[0042] S4: Secondary forging and drawing, the steel ingot in S3 is returned to the furnace and heated to forge and draw the slab again, the deformatio...
PUM
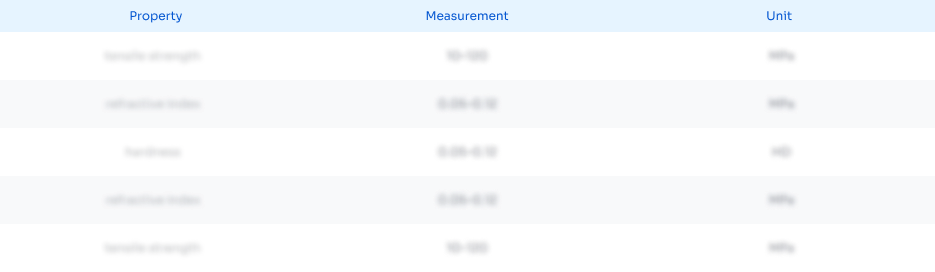
Abstract
Description
Claims
Application Information

- R&D
- Intellectual Property
- Life Sciences
- Materials
- Tech Scout
- Unparalleled Data Quality
- Higher Quality Content
- 60% Fewer Hallucinations
Browse by: Latest US Patents, China's latest patents, Technical Efficacy Thesaurus, Application Domain, Technology Topic, Popular Technical Reports.
© 2025 PatSnap. All rights reserved.Legal|Privacy policy|Modern Slavery Act Transparency Statement|Sitemap|About US| Contact US: help@patsnap.com