Anti-crack manufacturing method of duplex stainless steel F53 forging forming
A duplex stainless steel, forging molding technology, applied in the direction of manufacturing tools, forging/pressing/hammer devices, heating/cooling equipment, etc., can solve the problems of low forging efficiency, high energy consumption, low efficiency, etc. The effect of reducing energy consumption and improving performance
- Summary
- Abstract
- Description
- Claims
- Application Information
AI Technical Summary
Problems solved by technology
Method used
Examples
Embodiment 1
[0016] Embodiment 1: A kind of manufacturing method of duplex stainless steel F53 forging forming anti-crack, its steps are:
[0017] ①Put the steel ingot into the heating furnace, install the furnace to avoid direct flame injection, heat with the furnace at less than 60°C / h, and keep it warm for 4 hours at 300°C-350°C;
[0018] ② After 4 hours of heat preservation, the steel ingot with a temperature of 300°C to 350°C is raised to 1020°C to 1050°C at a rate of 100°C / h, and held for 20 hours;
[0019] ③Heat the steel ingot with a temperature of 1020°C to 1050°C at a rate of 70°C / h to 100°C / h to 1200°C and keep it warm for 20 hours;
[0020] ④Take out the steel ingot obtained in step ③ and put it on the forging machine. Use the forging head with an arc-shaped bottom to lightly tap the steel ingot to round and chamfer the corners, straight upsetting, and the single pressing amount of the forging head of the forging machine is less than 30mm. Seconds, each time the forging direct...
PUM
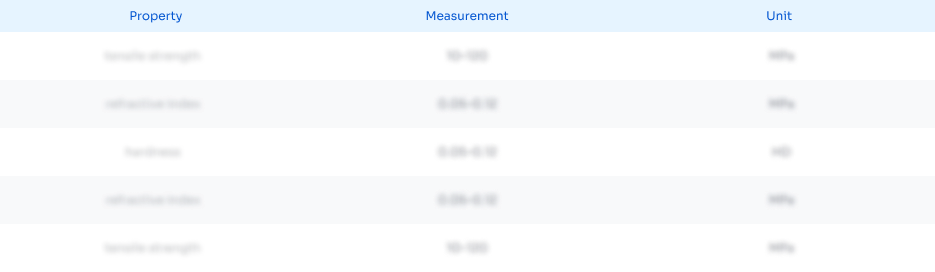
Abstract
Description
Claims
Application Information

- R&D Engineer
- R&D Manager
- IP Professional
- Industry Leading Data Capabilities
- Powerful AI technology
- Patent DNA Extraction
Browse by: Latest US Patents, China's latest patents, Technical Efficacy Thesaurus, Application Domain, Technology Topic, Popular Technical Reports.
© 2024 PatSnap. All rights reserved.Legal|Privacy policy|Modern Slavery Act Transparency Statement|Sitemap|About US| Contact US: help@patsnap.com