Precision machining control method and machining die for single-layer closed wave spring
A wave spring and precision machining technology, applied in the field of parts processing, can solve problems such as difficult to meet the requirements of scientific research and production tasks of key models, unable to meet the service requirements of wave springs, large permanent deformation of wave springs, etc., to achieve stable dimensions, reliable mechanical properties, The full effect of organizational transformation
- Summary
- Abstract
- Description
- Claims
- Application Information
AI Technical Summary
Problems solved by technology
Method used
Image
Examples
Embodiment
[0044] The precision machining control method for a single-layer closed wave spring provided in this embodiment includes the following steps:
[0045] 1) Making the blank, according to the design drawing of the part to be processed, the raw material is made into a ring-shaped blank with a die;
[0046] In this step, the punching die is a down-loading composite die, which is punched in the flattened state of the strip, and the dimensional accuracy of the workpiece is higher than that of commonly used flip-chip composite die punching, wire electric discharge cutting, laser cutting, etc. Blank method; raw materials are steel plates or steel strips of 65Mn type;
[0047] 2) cold stamping forming of ring-shaped blanks to obtain rough machined parts;
[0048] 2.1) Install the special stamping die on the crank press;
[0049] 2.2) Place the ring-shaped blank made in step 1) in the positioning ring of the forming die, position it with the shape of the ring-shaped blank, adjust the s...
Embodiment 2
[0074] see figure 1 , a stamping mold for realizing the precision machining control method of a single-layer closed wave spring, including an upper mold 16, a lower mold 17, and a positioning ring 18; the upper mold 16 and the lower mold 17 are arranged relative to each other from top to bottom; The outer edge and the two are in clearance fit; the positioning ring 18 can move up and down freely along the axial direction of the lower die 17; the positioning ring 18 is provided with a pick-up groove for placing the blank and taking out the workpiece; when the upper die 16 and the lower die 17 are in contact, Form the cavity mold. In order to keep the stability of the upper mold 16 and the lower mold 17, the stamping mold used in the present invention also includes a lower template 11, a lower mold fixed plate 12, an upper mold fixed plate 13, an upper template 14 and an anti-rotation pin 15, specifically connected The method is: the lower die 17 is fixed on the lower template 1...
Embodiment 3
[0077] see figure 2 , the correction mold provided in this embodiment includes a punch 21, a flat plate 22 and a base 24, the punch 21 is fixed on the press slider, and the flat plate 22 is connected with the base 24 by screws 23, and fixed on the press table. The luminosity of the working surfaces of the punch 21 and the flat plate 22 are all below Ra0.4 μm, so as to prevent defects caused by high friction between the flat plate 22 and the workpiece during calibration.
[0078] In this embodiment, a universal leveling mold is used to adjust the prefabricated height dimension of the waveform, effectively reducing the number of mold repairs of the pressing mold, and saving mold manufacturing costs.
PUM
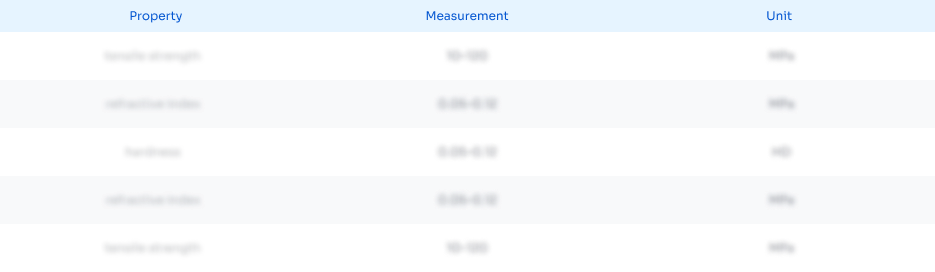
Abstract
Description
Claims
Application Information

- R&D
- Intellectual Property
- Life Sciences
- Materials
- Tech Scout
- Unparalleled Data Quality
- Higher Quality Content
- 60% Fewer Hallucinations
Browse by: Latest US Patents, China's latest patents, Technical Efficacy Thesaurus, Application Domain, Technology Topic, Popular Technical Reports.
© 2025 PatSnap. All rights reserved.Legal|Privacy policy|Modern Slavery Act Transparency Statement|Sitemap|About US| Contact US: help@patsnap.com