Method for packaging pressure sensor with multiple fine leads
A pressure sensor and packaging method technology, applied in microstructure devices, manufacturing microstructure devices, piezoelectric/electrostrictive/magnetostrictive devices, etc. Effects of biocompatibility and use stability, simple preparation process, and good thermal matching
- Summary
- Abstract
- Description
- Claims
- Application Information
AI Technical Summary
Problems solved by technology
Method used
Image
Examples
Embodiment Construction
[0049] In order to express the present invention more clearly, the present invention will be further described below in conjunction with the accompanying drawings.
[0050] In the following description, general example details are given in order to provide a deeper understanding of the present invention. Apparently, the described embodiments are only some of the embodiments of the present invention, not all of them. It should be understood that the specific examples are only used to explain the present invention, not to limit the present invention.
[0051] It should be understood that when the terms "comprising" and or "comprising" are used in this specification, they indicate the presence of the stated features, integers, steps, operations, elements or components, but do not exclude the presence or addition of one or more other Features, integers, steps, operations, elements, components or combinations thereof.
[0052]As mentioned in the background art, silicon microsenso...
PUM
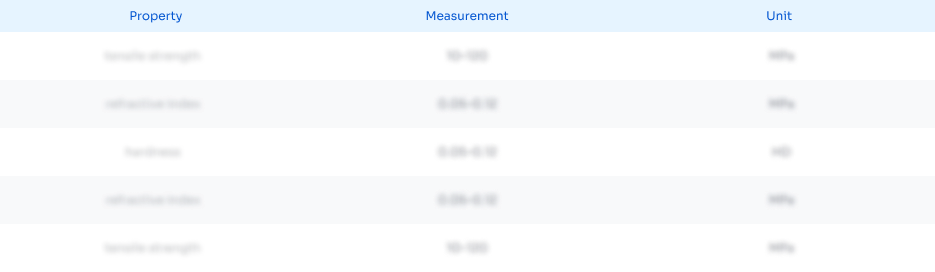
Abstract
Description
Claims
Application Information

- R&D Engineer
- R&D Manager
- IP Professional
- Industry Leading Data Capabilities
- Powerful AI technology
- Patent DNA Extraction
Browse by: Latest US Patents, China's latest patents, Technical Efficacy Thesaurus, Application Domain, Technology Topic, Popular Technical Reports.
© 2024 PatSnap. All rights reserved.Legal|Privacy policy|Modern Slavery Act Transparency Statement|Sitemap|About US| Contact US: help@patsnap.com