Aggregation-type composite powder for high-temperature abradable seal coating layer and preparing method of aggregation-type composite powder
A sealing coating and composite powder technology, which is applied in the field of agglomerated composite powder for high-temperature abradable sealing coating and its preparation method, and can solve the problems of poor thermal matching, shedding, and high-temperature oxidation resistance of superalloy substrates Insufficiency and other problems, to achieve the effect of improving the uniformity of tissue performance, increasing the service life, and good thermal matching
- Summary
- Abstract
- Description
- Claims
- Application Information
AI Technical Summary
Problems solved by technology
Method used
Examples
Embodiment 1
[0028] Raw material composition: structural component: β-NiAl intermetallic compound; abradable component: polyphenylene; adhesive: polyvinylpyrrolidone.
[0029] Raw material ratio: 5wt% of abradable components, 1wt% of adhesives, and the balance of structural components.
[0030] Preparation method: Mix the structural component and the wearable component by ball milling for more than 12 hours. After the components are evenly mixed, take out the powder for use. The binder is then added while stirring. When stirring, use a "one-shaped" stirring paddle with a length of 30-50 cm, and a flat-bottomed mixing tank with an inner diameter of 40-80 cm. The thickness of the material must not exceed one-third of the height of the inner diameter of the mixing tank. min. The binder is added at one time. Continue to stir the material until the raw material powder is agglomerated into granules. Use a 30-mesh screen to sieve the granulated powder, and put the sieved material back into the...
Embodiment 2
[0032] Raw material composition: structural component: mixture of β-NiAl intermetallic compound and MCrAlY alloy powder, the weight ratio of β-NiAl intermetallic compound and MCrAlY alloy powder is 1:1; abradable component: polyamide and hexagonal boron nitride A mixture of polyamide and hexagonal boron nitride in a weight ratio of 10:1; adhesive: A-B glue.
[0033] Raw material ratio: 10wt% of abradable components, 2wt% of adhesives, and the balance of structural components.
[0034] Preparation method: Mechanically stir and mix the structural component and the wearable component for more than 12 hours. After the components are evenly mixed, take out the powder for use. binder. When stirring, use a "one-shaped" stirring paddle with a length of 30-50 cm, and a flat-bottomed mixing tank with an inner diameter of 40-80 cm. The thickness of the material must not exceed one-third of the height of the inner diameter of the mixing tank. min. The binder is added at one time. Stir...
Embodiment 3
[0036] Raw material composition: structural component: mixture of β-NiAl intermetallic compound and MCrAlY alloy powder, the weight ratio of β-NiAl intermetallic compound and MCrAlY alloy powder is 3:1; abradable component: polyamide and hexagonal boron nitride A mixture of polyamide and hexagonal boron nitride in a weight ratio of 3:1; adhesive: alkyd varnish.
[0037] Raw material ratio: 15wt% of abradable components, 3wt% of adhesives, and the balance of structural components.
[0038] Preparation method: Mix the structural component and the wearable component by ball milling for more than 12 hours. After the components are evenly mixed, take out the powder for use. binder. When stirring, use a "one-shaped" stirring paddle with a length of 30-50 cm, and a flat-bottomed mixing tank with an inner diameter of 40-80 cm. The thickness of the material must not exceed one-third of the height of the inner diameter of the mixing tank. min. The binder is added in two times, the fi...
PUM
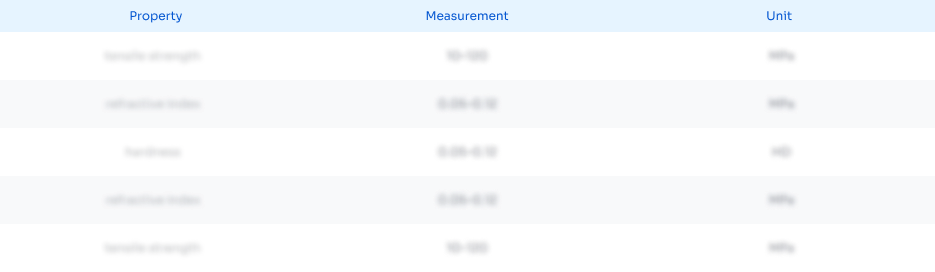
Abstract
Description
Claims
Application Information

- R&D
- Intellectual Property
- Life Sciences
- Materials
- Tech Scout
- Unparalleled Data Quality
- Higher Quality Content
- 60% Fewer Hallucinations
Browse by: Latest US Patents, China's latest patents, Technical Efficacy Thesaurus, Application Domain, Technology Topic, Popular Technical Reports.
© 2025 PatSnap. All rights reserved.Legal|Privacy policy|Modern Slavery Act Transparency Statement|Sitemap|About US| Contact US: help@patsnap.com