Sodium carboxymethyl cellulose and preparation method thereof, and battery negative electrode slurry and preparation method thereof
A technology of sodium carboxymethyl cellulose and negative electrode slurry, which is applied in the direction of battery electrodes, circuits, electrical components, etc., can solve problems such as scratches, affecting battery safety, blocking filter elements, etc., achieves stable coating surface density and saves production cost, effect of rapid viscosity release
- Summary
- Abstract
- Description
- Claims
- Application Information
AI Technical Summary
Problems solved by technology
Method used
Image
Examples
preparation example Construction
[0024] The invention provides a kind of preparation method of sodium carboxymethyl cellulose, comprising the following steps:
[0025] The crude product of sodium carboxymethyl cellulose is obtained through alkalization and etherification of natural cellulose in sequence, and sodium carboxymethyl cellulose is prepared through the processes of neutralization, washing, stripping, drying and pulverization in sequence;
[0026] Among them, in one or more processes of neutralization, washing, steam stripping, drying, and pulverization, or in sodium carboxymethyl cellulose, fast solvent is added for reaction; preferably in the three processes of neutralization, washing, and steam stripping Add fast solvent to carry out the reaction.
[0027] Preferably, in parts by weight, alkalization: 1 part of cellulose, 0.7-3 parts of liquid caustic soda and 1-10 parts of alcohol mixture in a reaction kettle, alkalized at 10-55°C for 0.5-3 hours to form alkali fibers white.
[0028] Etherifica...
Embodiment 1
[0050] In parts by weight, alkalization: 1 part of cellulose, 2 parts of potassium hydroxide solution and 7 parts of alcohol mixture in a reaction kettle, alkalized at 45 ° C for 2 hours to form alkali cellulose;
[0051] Etherification: Add 2 parts of the mixture of chloroacetic acid and alcohol after alkalization, and control the temperature at 40°C for 0.5 hours in the initial stage of etherification; in the middle stage of etherification, control the temperature at 50°C for 1 hour; in the later stage of etherification, the temperature Control at 70°C for 1 hour to obtain a crude product of sodium carboxymethylcellulose.
[0052] Neutralization: Add 80 parts of alcohol-water mixture to the crude product after the reaction, and stir for 1.5 hours, during which a pH regulator is added to neutralize the residual alkali.
[0053] Washing: The neutralized crude sodium carboxymethyl cellulose product is washed three times with a mixture of alcohol and water to remove reaction by-pr...
Embodiment 2
[0059] The processes of alkalization, etherification, neutralization, washing, stripping, drying and pulverization are the same as in Example 1.
[0060] The crude product of sodium carboxymethyl cellulose is obtained through alkalization and etherification of natural cellulose in sequence, and then sodium carboxymethyl cellulose is prepared through the processes of neutralization, washing, stripping, drying and pulverization in sequence. Among them, the first-stage fast solvent (oxalic acid) is added in the neutralization process to adjust the pH to neutral; the second-stage fast solvent (glyoxal and polyethylene oxide) is added during the stripping process.
[0061] Wherein, the first-stage fast solvent addition quality is 5% of the crude product of sodium carboxymethyl cellulose, and reacts at 30° C. for 20 min; the second-stage quick solvent addition quality is 14% of the crude product of sodium carboxymethyl cellulose, and (The mass ratio of glyoxal to polyethylene oxide ...
PUM
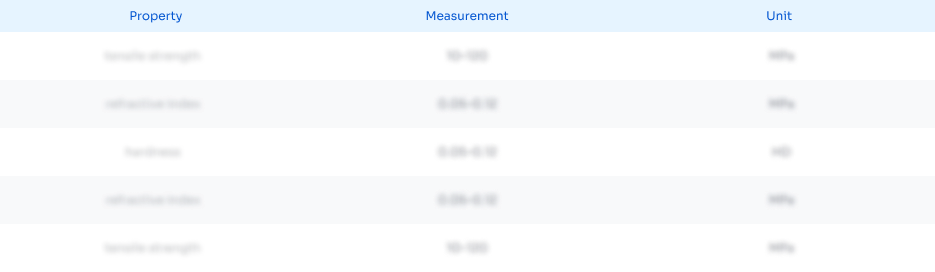
Abstract
Description
Claims
Application Information

- R&D Engineer
- R&D Manager
- IP Professional
- Industry Leading Data Capabilities
- Powerful AI technology
- Patent DNA Extraction
Browse by: Latest US Patents, China's latest patents, Technical Efficacy Thesaurus, Application Domain, Technology Topic, Popular Technical Reports.
© 2024 PatSnap. All rights reserved.Legal|Privacy policy|Modern Slavery Act Transparency Statement|Sitemap|About US| Contact US: help@patsnap.com