Low-pressure precision casting method for magnesium alloy thin-wall shell part
A thin-walled shell, precision casting technology, applied in casting molding equipment, casting molds, casting mold components, etc., can solve the problem of many casting defects such as oxidation slag inclusion, avoid cold insulation and under-casting defects, and achieve good fluidity. , the effect of improving product quality and yield
- Summary
- Abstract
- Description
- Claims
- Application Information
AI Technical Summary
Problems solved by technology
Method used
Image
Examples
Embodiment 1
[0024] The profile size of a certain magnesium alloy cylindrical thin-walled part prepared in this example is The wall thickness is 3-10mm, and has internal structures such as through holes and pipelines. Concrete preparation process steps are as follows:
[0025] (1) Use UG software to design parts casting drawings, design and manufacture aluminum wax molds according to the parts casting drawings, use medium temperature wax, press wax patterns and runners, weld runners and wax patterns, and weld molds after assembly The team conducts inspection, correction and repair;
[0026] (2) On the surface of the wax model, brush a layer of 320-mesh corundum powder and silica sol mixed paint with a weight ratio of 3:1, and then hang a layer of 100-mesh corundum powder, hang it once and dry it; hang the corundum powder repeatedly 4 layers , the shell was dried for 12 hours, and then steam dewaxed at 160°C and 5 atmospheres, and the shell was baked at 900°C for 5 hours and then cooled ...
Embodiment 2
[0032] (1) Use UG software to design parts casting drawings, design and manufacture aluminum wax molds according to the parts casting drawings, use medium temperature wax, press wax patterns and runners, weld runners and wax patterns, and weld molds after assembly The team conducts inspection, correction and repair;
[0033] (2) On the surface of the wax model, brush a layer of 320-mesh corundum powder and silica sol mixed paint with a weight ratio of 3:1, and then hang a layer of 100-mesh corundum powder, hang it once, dry it, and hang the corundum powder repeatedly 4 layers , the shell was dried for 12 hours, and then steam dewaxed at 160°C and 5 atmospheres, and the shell was baked at 900°C for 5 hours and then cooled with the furnace; drilled on the top of the shell and the corners where gas is easy to accumulate The exhaust hole of the mold shell is rinsed with 5wt.% boric acid aqueous solution, repeated 3 times, and then put into the furnace and dried at 300°C for 3 hou...
PUM
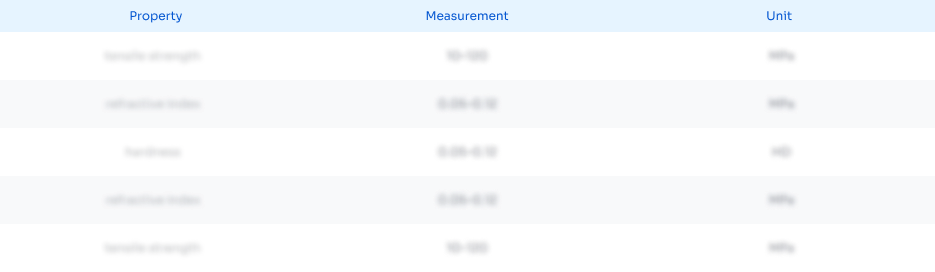
Abstract
Description
Claims
Application Information

- R&D Engineer
- R&D Manager
- IP Professional
- Industry Leading Data Capabilities
- Powerful AI technology
- Patent DNA Extraction
Browse by: Latest US Patents, China's latest patents, Technical Efficacy Thesaurus, Application Domain, Technology Topic, Popular Technical Reports.
© 2024 PatSnap. All rights reserved.Legal|Privacy policy|Modern Slavery Act Transparency Statement|Sitemap|About US| Contact US: help@patsnap.com