Rolling process of F type rail groove rolling system
A pass type and process technology, applied in the direction of rolling force/roll gap control, metal rolling, etc., can solve the problems of unfavorable metal flow, increase the size of F-shaped steel blank, and not easy to fill, etc., to achieve convenient cross-sectional shape and size of finished products , high yield and easy operation
- Summary
- Abstract
- Description
- Claims
- Application Information
AI Technical Summary
Problems solved by technology
Method used
Image
Examples
Embodiment Construction
[0023] The present invention will be described in further detail below in conjunction with specific embodiments, so that those skilled in the art can understand.
[0024] Such as Figure 2~3 The rolling process of the shown F-rail rolling pass system comprises the following steps:
[0025] 1) Using the universal pass mode, the upper horizontal roll 1, the lower horizontal roll 2, and the two vertical rolls 3 in the horizontal direction compress and deform the rolled piece 4 from four directions, so that the metal can fill the entire pass; among them, the universal pass Mode reduction is 6mm and compression ratio is 25%;
[0026] 2) The edging machine adopts a two-roll pass pattern, and the upper roll 5 and the lower roll 6 finish the corners of the rolled piece 4; among them, the chamfer R of the rolled piece corner is 8-12mm, and the finished roll gap Set to 10 ~ 14mm.
[0027] 3) The "universal mode" and "two-roll mode" are used to repeatedly alternate rolling to ensure t...
PUM
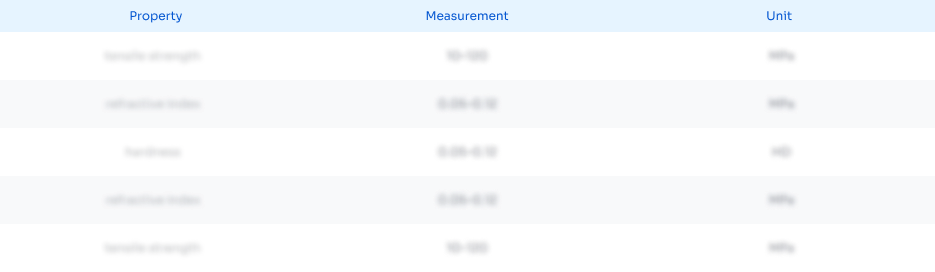
Abstract
Description
Claims
Application Information

- R&D Engineer
- R&D Manager
- IP Professional
- Industry Leading Data Capabilities
- Powerful AI technology
- Patent DNA Extraction
Browse by: Latest US Patents, China's latest patents, Technical Efficacy Thesaurus, Application Domain, Technology Topic, Popular Technical Reports.
© 2024 PatSnap. All rights reserved.Legal|Privacy policy|Modern Slavery Act Transparency Statement|Sitemap|About US| Contact US: help@patsnap.com