Polypropylene plastic mold for concrete member and preparation method of polypropylene plastic mold
A polypropylene plastic and concrete technology, applied in the field of concrete components, can solve the problems of poor toughness and rigidity, poor wear resistance, deformation, and affecting the stability of concrete components, so as to improve heat resistance, not easily damaged and deformed, and improve toughness and Rigid effect
- Summary
- Abstract
- Description
- Claims
- Application Information
AI Technical Summary
Problems solved by technology
Method used
Image
Examples
Embodiment 1
[0030] Put 80 parts of PP, 5 parts of mass compatibilizer PP-g-MAH, 15 parts of POE-g-MAH into a blast drying oven (set to 60 ° C) to dry for 24 hours, then add 10 parts of 15 μm in diameter, Basalt fibers with a length of 18 mm, as well as an appropriate amount of nucleating agent and antioxidant, were added to a twin-screw extruder and mixed uniformly for melt blending and extrusion experiments.
[0031] The temperature of the five zones of the twin-screw extruder is 190°C, 200°C, 210°C, 180°C, and 160°C, respectively, the head temperature is 150°C, and the screw speed is 120 rpm. The extruded strips are water-cooled, blown dry, sent to the pelletizer and adjusted to 200r / min for pelletizing, and pellets are prepared for use.
[0032] After melt blending and extrusion granulation, the obtained pellets were dried in a drying oven at a constant temperature of 60° C. for 12 hours, and then an injection molding experiment was performed.
Embodiment 2
[0034] The implementation steps are the same as in Example 1, but the addition amount of each component is different, 75 parts of PP, 10 parts of PP-g-MAH, 10 parts of POE-g-MAH, 15 parts of basalt fibers with a diameter of 15 μm and a length of 18 mm, and an appropriate amount. nucleating agent and antioxidant.
Embodiment 3
[0036] The implementation steps are the same as in Example 1, but the addition amount of each component is different, 60 parts of PP, 15 parts of PP-g-MAH, 15 parts of POE-g-MAH, 20 parts of basalt fibers with a diameter of 15 μm and a length of 18 mm, and an appropriate amount. nucleating agent and antioxidant.
PUM
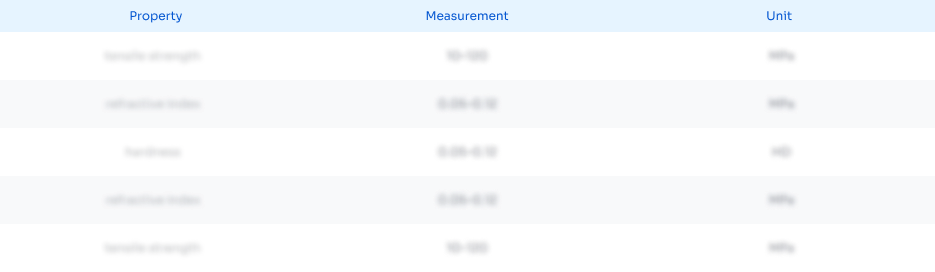
Abstract
Description
Claims
Application Information

- R&D Engineer
- R&D Manager
- IP Professional
- Industry Leading Data Capabilities
- Powerful AI technology
- Patent DNA Extraction
Browse by: Latest US Patents, China's latest patents, Technical Efficacy Thesaurus, Application Domain, Technology Topic, Popular Technical Reports.
© 2024 PatSnap. All rights reserved.Legal|Privacy policy|Modern Slavery Act Transparency Statement|Sitemap|About US| Contact US: help@patsnap.com