Stainless steel embossing etching process
A technology of stainless steel and stainless steel plate, applied in printing process, process for producing decorative surface effects, decorative arts, etc., can solve the problems of narrow application range of embossing equipment, inaccessibility, defective products, etc.
- Summary
- Abstract
- Description
- Claims
- Application Information
AI Technical Summary
Problems solved by technology
Method used
Image
Examples
Embodiment 1
[0037] refer to Figure 1-6 , a stainless steel embossing etching process, specifically comprises the following steps:
[0038] S1, pre-treatment: firstly carry out pre-degreasing treatment and deoxidation film treatment on the surface of the stainless steel plate to be etched, then wash and dry it;
[0039] S2. Screen printing: screen-print the stainless steel plate in S1, fix the nylon monofilament mesh on the screen frame with a stretcher, scrape and apply photosensitive glue through the paddle, and after the coating film is dried, it will be The prepared patterned black and white film is attached to the coated silk screen, and after exposure and development, the screen printing template is made, and the screen printing is dried after completion;
[0040] S3, making patterns: fix the stainless steel plate and the silk screen template in S2 on the corresponding position of the screen printing machine, use ink to print the patterns and then dry them;
[0041] S4. Post-proce...
Embodiment 2
[0051] refer to Figure 6 , a stainless steel embossing etching process, the same material guide plate 35 is connected between the inner walls on both sides of the installation plate 1 through bearing rotation, the material guide plate 35 is arranged at the rear end of the first embossing roller 9, behind the installation plate 1 The end is hinged with a sleeve rod 36, and the bottom of the sleeve rod 36 is provided with an embedding groove 37, and the inner wall of the front end of the embedding groove 37 is fixed with a return spring 38 by a bolt, and the rear end of the return spring 38 is fixed with an inner rod 39 by a bolt, and the inner rod 39 and the material guide plate Hinged between 35.
[0052] Further, the inner walls on both sides of the embedding groove 37 are provided with limiting grooves 40, and the limiting grooves 40 are slidingly connected with the limiting blocks 41, and the limiting blocks 41 and the inner rods 39 are fixed by bolts, so that the inner ro...
Embodiment 3
[0055] refer to Figure 7-8 , a stainless steel embossing etching process, the front end of the supporting plate 7 is fixed with an adjustment plate 42 by bolts, the top of the adjustment plate 42 is provided with an adjustment groove 43, and two symmetrically distributed adjustment blocks 44 are slidingly connected in the adjustment groove 43. The adjustment block 44 The top is fixed with a support rod 45 by bolts, and the rear end of the support rod 45 is fixed with a positioning plate 46 by bolts. In the adjustment groove 43, a two-way screw rod 47 is connected through bearing rotation. Blanking.
[0056] Further, the top of the supporting plate 7 is provided with a plurality of evenly distributed grooves 48, the same inner shaft 49 is rotatably connected between the inner walls on both sides of the groove 48 through bearings, and a sleeve 50 is sleeved and fixed on the inner shaft 49, that is, Can reduce frictional resistance.
[0057] Working principle: When in use, pla...
PUM
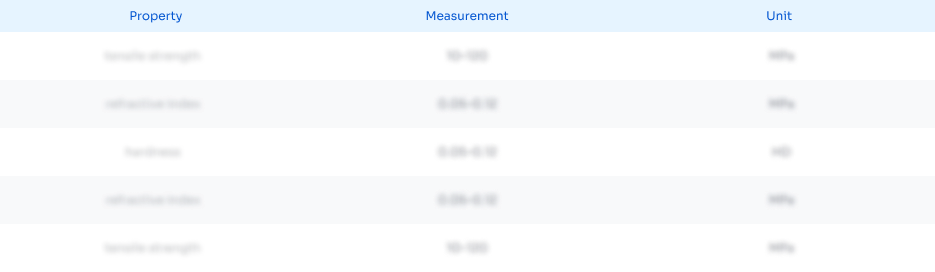
Abstract
Description
Claims
Application Information

- R&D Engineer
- R&D Manager
- IP Professional
- Industry Leading Data Capabilities
- Powerful AI technology
- Patent DNA Extraction
Browse by: Latest US Patents, China's latest patents, Technical Efficacy Thesaurus, Application Domain, Technology Topic, Popular Technical Reports.
© 2024 PatSnap. All rights reserved.Legal|Privacy policy|Modern Slavery Act Transparency Statement|Sitemap|About US| Contact US: help@patsnap.com