Preparation method of quantum dot modified nanosheet composite material
A technology of composite materials and quantum dots, applied in chemical instruments and methods, electrodes, electrolytic processes, etc., can solve the problem of no carbon-based organic compounds, achieve simple equipment, broad application prospects, and improve oxygen evolution performance
- Summary
- Abstract
- Description
- Claims
- Application Information
AI Technical Summary
Problems solved by technology
Method used
Image
Examples
Embodiment 1
[0037] (1) Preparation of ferric oxide nanotubes: Weigh 1000 mg of anhydrous ferric chloride and 46 mg of ammonium dihydrogen phosphate, respectively, and disperse them in 20 mL of deionized water, and process with ultrasonic stirring. Measure 80 mL of deionized water and add 3 mL of trichloride in turn. Ferric chloride solution and 2mL ammonium dihydrogen phosphate solution were vigorously stirred and mixed, and the mixture was transferred to a reaction kettle. After the shell was packaged, it was transferred to an oven, kept at a constant temperature of 220°C for 30 hours, and cooled naturally. The obtained product was centrifugally washed, and then The product was dispersed into 20 mL of deionized water, and the resulting dispersion was subjected to freezing treatment, and finally transferred to a freeze dryer for freeze-drying to obtain ferric oxide nanotubes.
[0038](2) Preparation of nickel-cobalt hydroxide / ferric oxide nanotube composite material: Disperse 0.1 g of ferr...
Embodiment 2
[0042] (1) Preparation of ferric oxide nanotubes: Weigh 1622 mg of anhydrous ferric chloride and 46 mg of ammonium dihydrogen phosphate, respectively, and disperse them in 20 mL of deionized water. Water ferric chloride solution and 2.88mL ammonium dihydrogen phosphate solution were vigorously stirred and mixed, and the mixture was transferred to a reaction kettle. After the shell was packaged, it was transferred to an oven, kept at a constant temperature of 220°C for 36 hours, and cooled naturally. After centrifuging and washing, the product was dispersed into 20 mL of deionized water, and the resulting dispersion was subjected to freezing treatment, and finally transferred to a freeze dryer for freeze drying to obtain ferric oxide nanotubes.
[0043] (2) Preparation of nickel-cobalt hydroxide / ferric oxide nanotube composite material: disperse 0.05 g of ferric oxide nanotubes obtained in step (1) into 10 mL of deionized water for ultrasonic treatment, and weigh 365.4 mg of nic...
Embodiment 3
[0047] (1) Preparation of ferric oxide nanotubes: Weigh 1622 mg of anhydrous ferric chloride and 46 mg of ammonium dihydrogen phosphate, respectively, and disperse them in 20 mL of deionized water. Ferric chloride solution and 2.88mL ammonium dihydrogen phosphate solution were vigorously stirred and mixed, and the mixture was transferred to a reaction kettle. After the shell was packaged, it was transferred to an oven, kept at a constant temperature of 220°C, kept for 48 hours, and the obtained product was centrifugally washed by natural cooling. Afterwards, the product was dispersed into 20 mL of deionized water, and the resulting dispersion was subjected to freezing treatment, and finally transferred to a freeze dryer for freeze drying to obtain ferric oxide nanotubes.
[0048] (2) Preparation of nickel-cobalt hydroxide / ferric oxide nanotube composite material: disperse 0.05 g of ferric oxide obtained in step (1) into 10 mL of deionized water for ultrasonic treatment, weigh 1...
PUM
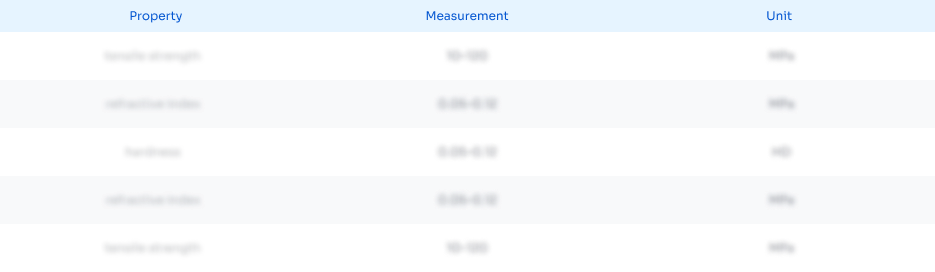
Abstract
Description
Claims
Application Information

- Generate Ideas
- Intellectual Property
- Life Sciences
- Materials
- Tech Scout
- Unparalleled Data Quality
- Higher Quality Content
- 60% Fewer Hallucinations
Browse by: Latest US Patents, China's latest patents, Technical Efficacy Thesaurus, Application Domain, Technology Topic, Popular Technical Reports.
© 2025 PatSnap. All rights reserved.Legal|Privacy policy|Modern Slavery Act Transparency Statement|Sitemap|About US| Contact US: help@patsnap.com