Screen printing plate with high adhesion and manufacturing process thereof
A production process and adhesive technology, applied in printing process, printing plate preparation, screen printing, etc., can solve the problems affecting the bonding strength of the steel mesh layer 12 and the polyester mesh layer 13, etc.
- Summary
- Abstract
- Description
- Claims
- Application Information
AI Technical Summary
Problems solved by technology
Method used
Image
Examples
Embodiment Construction
[0029] The content of the present invention will be further described in detail below in conjunction with the accompanying drawings.
[0030] like Image 6 As shown, a screen with strong adhesiveness includes an annular frame body 1, an annular connecting net 2, a screen printing mesh 3, an annular adhesive layer 5, and a polymer engraving film 4; the annular connecting net 2 includes a bottom ring Net 231, up and down accepting ring net 22, upper ring net 21; described up and down accepting ring net 22 is installed between the upper ring net 21 and the bottom ring net 231; the lower end of the described up and down accepting ring net 22 is connected to the bottom ring net 231 around outside; the upper end of the upper and lower receiving ring net 22 is connected to the surrounding inner side of the upper ring net 21; the bottom ring net 231 and the upper and lower receiving ring net 22 jointly form a sunken accommodation tank 6; The lower end of the upper ring net 21 is conn...
PUM
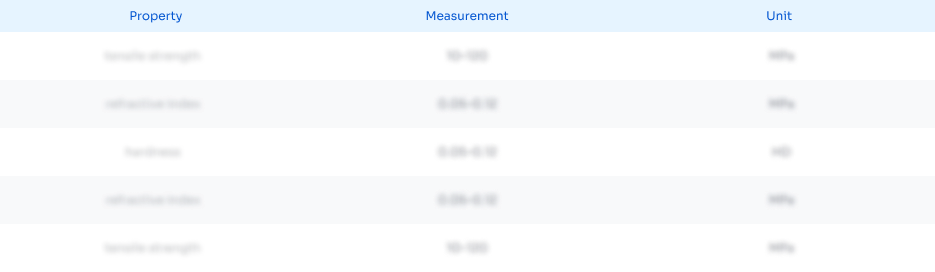
Abstract
Description
Claims
Application Information

- Generate Ideas
- Intellectual Property
- Life Sciences
- Materials
- Tech Scout
- Unparalleled Data Quality
- Higher Quality Content
- 60% Fewer Hallucinations
Browse by: Latest US Patents, China's latest patents, Technical Efficacy Thesaurus, Application Domain, Technology Topic, Popular Technical Reports.
© 2025 PatSnap. All rights reserved.Legal|Privacy policy|Modern Slavery Act Transparency Statement|Sitemap|About US| Contact US: help@patsnap.com